Proper pallet rack safety is vital to prevent accidents, injuries, and damage to inventory. In this article, we’ll discuss the importance of safety regulations, the key components of a safe pallet rack system, and how to prevent common safety hazards.
We’ll also talk about implementing effective warehouse safety policies and using safety accessories and equipment, all while learning from real-life incidents to ensure a safe and efficient warehouse environment.
Key Takeaways: Preventing Accidents
- Adhering to safety regulations and utilizing safety accessories are essential for preventing workplace accidents when using pallet racking systems.
- Proper design, installation, maintenance & inspection of pallet racks, as well as employee training and awareness, will reduce accident risks and promote a productive work environment.
- Implement effective warehouse policies, encourage open communication among employees, and regularly review/update safety protocols to ensure compliance with regulations and the success of operations.
Understanding Pallet Rack Safety
Pallet rack safety encompasses the safe use of racking systems and potential injuries that could occur in a workplace accident. When safety protocols for warehouse pallet racks are neglected, employees are exposed to potential hazards. Adherence to safety guidelines and regulations is paramount for maintaining warehouse efficiency and preventing accidents, injuries, and inventory damage.
Various safety accessories and equipment, such as column protectors and guards, safety panels and netting, and appropriate signage and markings, are available for use in a pallet racking system. These accessories significantly contribute to safety maintenance in and around pallet racks, minimizing accident risks.
Importance of Safety Regulations
Adhering to safety regulations ensures a safe working environment and avoids potential OSHA fines. These regulations encompass various aspects of pallet rack systems, such as regular inspections and maintenance, correct loading, undamaged and easily accessible racks, and employee safety training.
Following these guidelines allows warehouse managers to secure storage racks, palletize items, use pallet stops, limit the height of stored items, and adhere to installation instructions and safe stacking requirements.
Failure to comply with these regulations can result in significant consequences, including workplace accidents, damage to inventory, OSHA fines, and potential legal ramifications.
Compliance with safety regulations safeguards warehouse employees and promotes a well-organized, efficient storage facility.
Key Components of a Safe Pallet Rack System
To ensure safety in a pallet rack system, four key components must be considered: proper engineering design and installation, regular maintenance and inspection, and employee training and awareness. Proper installation is crucial to avoid pallet rack damage and collapses. Modular pallet racking designs offer flexibility. With the approval of an engineer, they can be easily adapted to accommodate new goods both vertically and horizontally.
To determine the rack load capacity of a pallet rack, it is best to consult the manufacturer regarding the entire system and components. The optimal choice is to have the manufacturer or a seismic engineer appraise the pallet rack, including the assembly procedure. Every racking system should have LARC documents that detail the Load Application Rack Capacity of your system.
Addressing these key components enables warehouse managers to maintain safe, efficient pallet rack systems that meet their facility’s storage needs. Prioritizing safety during the design, installation, maintenance, and training processes helps reduce accident risks and fosters a more productive work environment.
Proper Design and Installation
Ensuring pallet racks are designed and installed correctly is essential to prevent collapses and other safety hazards. Be sure that a certified engineer licensed in your state has approved your plans. Not all engineers are familiar with the design of pallet racking systems, so consult an engineer who specializes in pallet rack systems. They will give you comprehensive engineered design plans that will guide you in the installation and maintenance of your racking system.
Regular Maintenance and Inspection
Regular maintenance and inspection of pallet racks are essential to identify and address any potential issues before they become more serious. Regular execution of the plan is essential to keep the equipment in good working order. Consistent maintenance and inspection help ensure the racking systems are in optimal condition and safe to use.
By regularly reviewing and updating the maintenance plan, warehouse managers can ensure that their pallet racks remain in excellent condition and minimize the risk of accidents and damage to inventory. This proactive approach to maintenance not only protects employees but also contributes to a more efficient and well-organized storage facility.
At a minimum, there should be a professional third-party inspection of your facility once a year. Greater frequency is recommended based on the level of activity in your warehouse.
Employee Training and Awareness
Training is essential for decreasing the possibility of injury and harm in the vicinity of racking systems. Implementing training for employees on proper pallet rack usage and warehouse safety protocols can help reduce the risk of accidents and injuries.
By prioritizing employee training and awareness, warehouse managers can ensure that their staff is knowledgeable about safety procedures, which can ultimately lead to a safer and more efficient work environment. Providing employees with the necessary training and resources to perform their tasks safely is an investment in the overall success of the warehouse operation.
Preventing Common Pallet Rack Safety Hazards
Common pallet rack safety hazards include overloading, forklift collisions, and falling objects. Ensuring that aisles are wide enough for forklift operators to navigate easily and that employees know the traffic flow to avoid collisions is crucial for warehouse safety. To prevent these hazards, adhering to weight capacity guidelines is essential, as failure to do so can result in serious injury, damaged equipment, and destroyed inventory.
Common safety hazards in warehouses include:
- Slippery floors
- Poor lighting
- Pedestrian collisions with forklifts
- Falling objects
- Improper use of equipment
- Lack of proper training
Proper safety measures can protect employees and contribute to a more efficient and well-organized storage facility.
Overloading and Uneven Loading
Overloading and uneven loading occur when a pallet rack is loaded with an amount of weight that exceeds its design capacity or when the weight is not distributed evenly across the rack. To prevent overloading and uneven loading, it is important to adhere to manufacturer guidelines and regularly inspect racks for indications of strain.
The potential repercussions of overloading and uneven loading of pallet racks include:
- Structural damage
- Increased risk of accidents
- Product damage
- Diminished storage capacity
- Flexural-torsional deformation of upright columns
By addressing overloading and uneven loading, warehouse managers can minimize the risk of accidents and create a safer and more efficient storage environment.
Forklift Collisions
Forklift collisions can result in substantial damage to pallet racks and potential harm to operators and other personnel. Forklift collisions are by far the largest source of damage in a warehouse. Some effective measures to minimize forklift collisions include:
- Ensuring aisles are clear of obstacles and obstructions
- Providing operators with training in safe driving practices
- Implementing protective equipment such as column protectors, safety panels, and netting
- Using electronic collision devices
- Using cameras on the forklifts for backing up and placement accuracy
- Use of horns in blind intersections
- Backing alarms
By implementing these measures, you can significantly reduce the likelihood of forklift collisions, promote a safer working environment, and increase efficiency.
Falling Objects and Debris
Safety panels, netting, and proper loading techniques can reduce the risk of falling objects. Safety panels and netting are protective barriers designed to be installed around pallet racks. The correct approach to loading involves ensuring that the pallet racks are loaded evenly and not overloaded.
By utilizing safety panels and netting, warehouse managers can minimize the risk of falling objects and create a safer work environment for their employees. Implementing these safety measures not only protects employees from potential injury but also contributes to a more efficient and well-organized storage facility.
Implementing Effective Warehouse Safety Policies
Successful warehouse safety policies require well-defined protocols, open dialogue, and regular revisions. Implementing effective warehouse safety policies offers several advantages, including cost reductions due to decreased accidents and property damage, safeguarding employees from injuries, promoting transparency and reporting of safety incidents, fostering a learning atmosphere, augmenting worker loyalty, enhancing quality, ensuring adherence to laws and regulations, and providing a safe workplace.
By prioritizing the implementation of effective warehouse safety policies, warehouse managers can create a safer work environment and minimize the risk of accidents. Ensuring that employees are aware of and adhere to these policies not only protects them from potential harm but also contributes to the overall efficiency and success of the warehouse operation.
Encouraging Open Communication
Open communication is essential to ensure that employees can report safety concerns and incidents, thereby facilitating a culture of continual improvement. Fostering open communication has multiple advantages, such as:
- Increased compliance with safety guidelines
- Increased identification of unique safety issues
- Strengthened team cohesion
- Amplified efficiency
- Strengthened problem-solving capabilities
- Foster a culture of continuous improvement and collaboration
For instance, in the 1990s, Alcoa doubled its production when it implemented a robust safety program that had as its backbone rapid and accurate communication of all accidents. Each accident had to be reported to the CEO in 24 hours with a concomitant solution to the root cause of the safety issue. This attention to detail increased morale, decreased injury, and increased productivity.
Regularly Reviewing and Updating Policies
It is essential to regularly review and update safety policies to guarantee their effectiveness and compliance with current regulations. When reviewing and updating safety policies, it is essential to consider the relevant regulations, evaluate the efficiency of existing policies, and implement any required adjustments. Employee training and awareness are of paramount importance when considering safety policies, as they ensure that personnel are conscious of the policies and comprehend how to adhere to them.
Regularly reviewing and updating safety policies ensures that warehouse facilities stay safe and compliant with relevant regulations. This not only protects employees from potential harm but also contributes to the overall efficiency and success of the warehouse operation.
Pallet Rack Safety Accessories and Equipment
Pallet rack safety accessories and equipment can assist in avoiding accidents and heightening overall warehouse safety. Some safety devices that can be employed in a warehouse include:
- Pallet stoppers
- Safety bars
- Netting systems
- Column protectors
- Load capacity placards
These accessories significantly contribute to safety maintenance in and around pallet racks, minimizing accident risks.
Column Protectors and Guards
Column protectors and guards are shields designed to safeguard the uprights from potential damage caused by forklifts and other material-handling equipment. These protective devices offer a range of benefits in warehouse and industrial settings, including:
- Enhanced visibility
- Impact absorption
- Camouflaging of damage
- Material advantages
- Enhanced safety
By incorporating column protectors and guards into their pallet rack systems, warehouse managers can:
- Protect the structural integrity of their racks
- Prevent costly damage
- Improve the overall safety of the warehouse
- Extend the lifespan of the pallet racks
- Contribute to a more efficient storage solution
- Transfer impact energy to the protector’s independent anchors to the floor rather than to the rack itself.
Safety Panels and Netting
Safety panels and netting are designed to provide protection against objects falling off pallet racks and shield personnel from any debris. These protective barriers offer several advantages, including:
- Legal liability reduction
- Product safeguarding
- Heightened safety
- Increased productivity
They are available in a range of materials, sizes, and shapes, offering versatility and customization for various applications.
By integrating safety panels and netting into their pallet rack systems, warehouse managers can minimize the risk of falling objects and protect both their employees and inventory. These protective barriers not only contribute to a safer work environment but also help maintain the overall efficiency of the storage facility.
Proper Signage and Markings
Adequate signage and markings serve to direct employees and forklift operators, thereby minimizing the possibility of accidents. Examples of signage and markings include warning signs, aisle markers, and floor markings. Strategically positioning signage and markings in areas that are readily perceptible to personnel and forklift operators can help prevent accidents and injuries.
By ensuring proper signage and markings in their warehouse facilities, managers can provide clear guidance for employees and forklift operators, reducing the risk of accidents. Investing in these safety measures not only protects employees from potential harm but also contributes to a more efficient and well-organized work environment.
Case Studies: Learning from Real-Life Incidents
Case studies of real-life incidents can provide invaluable insights and lessons for enhancing pallet rack safety in your warehouse. By analyzing these incidents, warehouse managers can identify potential risks and implement safety measures to prevent similar occurrences in the future. Examples of real-life incidents include:
- Overloading of pallet racks
- Forklift collisions
- Falling objects and debris
- Improper design and installation
- Lack of employee training and awareness
Learning from these real-life incidents enables warehouse managers to refine their safety policies and procedures, creating a safer work environment for their employees.
Summary: Ensuring Warehouse Efficiency and Safety through Effective Pallet Rack Management
In conclusion, pallet rack safety is an essential aspect of warehouse management. By understanding the importance of safety regulations, implementing key components of a safe pallet rack system, preventing common safety hazards, and establishing effective warehouse safety policies, managers can create a safer and more efficient storage environment.
Additionally, by utilizing safety accessories and equipment and learning from real-life incidents, warehouse managers can continuously improve their safety protocols and protect their employees from potential harm. Prioritizing pallet rack safety not only contributes to a more efficient and well-organized work environment but also ensures the overall success of the warehouse operation.
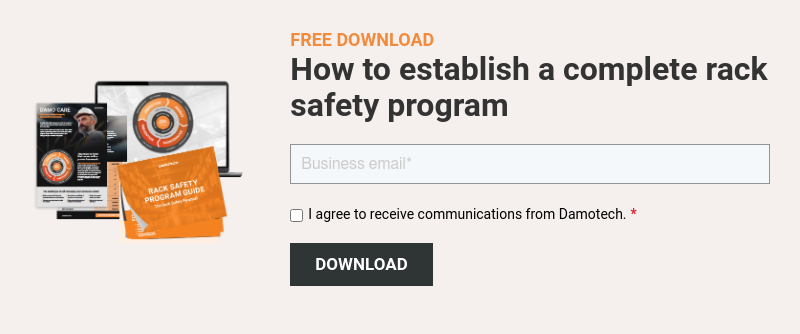
Frequently Asked Questions About OSHA Requirements and Racks
What are OSHA requirements for warehouse racking?
OSHA requires that racking must be 18 inches away from sprinklers for safety, and material stored in tiers must be stable with a 6:1 or lower height-to-depth ratio.
All materials stored in tiers must also be secured to prevent collapse, and the weight of stored materials must not exceed maximum safe load limits.
For a more detailed listing of OSHA rack requirements and the importance of preparing for an OSHA inspection, visit this page: https://www.damotech.com/rack-compliance-ebook-lp
What are the most important considerations with pallet racking?
When considering pallet racking, the two most important factors to consider are the dimensions of the pallet and the type of environment. Knowing these will help determine the depth and upright height of your warehouse racking.
What are the hazards associated with pallet racking?
Potential hazards associated with pallet racking include physical damage caused by lift truck collisions, misaligned racking, loose floor fittings, unsuitable forklift trucks, and overloaded racking systems.
How do you organize pallets in a warehouse?
Organize pallets in the warehouse by maximizing vertical space, blocking stacking when minimal pallets need to be stored, laying out a pallet rack system for maximum efficiency, and facing all rows in the same direction.
These strategies will ensure that inventory is easy to access and increase your storage capacity.
What is the importance of proper design and installation for pallet rack safety?
Proper design and installation of pallet racks are essential to ensure safety and prevent collapses and other hazardous incidents.