3. Use Racking Insight & Plan Work
Valuable insights play a pivotal role as they empower companies to make well-informed decisions on the best course of action to ensure the safety and reliability of warehouse racks. Armed with these pertinent insights, companies can effectively plan repairs based on issue priority levels, secure budgets and maintenance schedules, monitor progress and implement long-term strategies to prevent future issues.
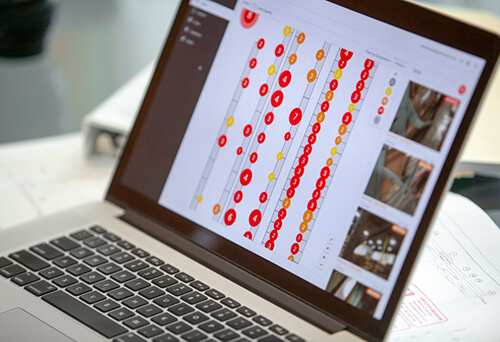
To effectively use information from rack inspections, insights are necessary to help understand the issues and find the best action. Engineering reports provide insights into the technical aspects of the inspection, including data on which components are most affected, recommendations for repairs, and the priority levels for corrective actions.
By harnessing safety management software, these insights are seamlessly translated into coordinated actions. These tools not only facilitate the transformation of insights but also enable continuous tracking of progress and the monitoring of key performance indicators (KPIs). Through the provision of comprehensive reports and timely status updates, these tools facilitate informed decision-making.
Engineering Report Insight
After each thorough inspection, rack experts write a detailed report based on their rigorous field observations, outlining their inspection procedures, findings, and recommendations for improving the safety and dependability of warehouse racks. An ideal report should contain the scope, key observations, identified issues with priority level and photo, and a proposed repair strategy and plan to address issues if requested.
As a best practice, it’s recommended to have the report stamped by a trained engineer. Leveraging the expertise of seasoned engineers ensures the report’s reliability and compliance with industry standards, which can be critical in ensuring the racks’ performance and preventing potential hazards. Additionally, this practice demonstrates due diligence and can sometimes be required by some regulations or certification bodies. Detailed reporting and prioritization of issues allow for appropriate corrective actions to address safety risks and return pallet racking to conformity.
Rack Maintenance Tracking and Planning
It’s crucial to have the right team in place and the necessary tools to monitor progress regarding warehouse safety. Having the right individuals with the expertise to effectively analyze the data and make informed decisions will ensure the success of the rack safety program. It includes tracking key performance indicators (KPIs) and defining a plan to address any issues highlighted in the reports.
Rack inspection and maintenance software plays a pivotal role in upholding efficiency and safety within warehouse operations. Online accessibility to inspection reports streamlines maintenance management, progress tracking, repair planning, and informed decision-making. The software should intricately capture and document racking issues, remotely monitor the condition of racking systems, and efficiently manage data from diverse locations, thereby centralizing inspection information for effortless retrieval. Moreover, by preserving engineering reports over time, it aids in maintaining historical records of past inspections and the evolving states of racking systems over the years.