Enhancing warehouse safety and efficiency with pallet rack load capacities and LARCs
Pallet racks are designed to store heavy goods and materials, and exceeding their load capacities can lead to catastrophic consequences such as rack collapse or material damage. The foremost reason warehouse managers prioritize pallet rack load capacities and LARCs is to ensure the safety of personnel and protect valuable inventory. Warehouse managers can prevent accidents, injuries, and potential lawsuits by understanding rack weight capacities and adhering to the manufacturer's guidelines or those outlined by qualified engineers. LARCs provide detailed drawings that depict racks' appropriate configuration and placement, highlighting weight capacities and other critical factors. These drawings are invaluable references for warehouse managers, enabling them to maintain their storage systems with utmost precision.
Warehouse racking space optimization
Optimizing warehouse space utilization is another crucial reason why pallet rack load capacities and LARCs are vital for warehouse managers. A comprehensive understanding of load capacities allows managers to maximize their facility's vertical and horizontal storage potential. By knowing the weight limits of each rack, managers can efficiently allocate storage space, eliminate inefficiencies, and reduce the need for additional racks or storage areas. LARCs play a pivotal role in this regard, as they provide detailed configurations that account for each rack component's dimensions and load-bearing capabilities. With this information, warehouse managers can optimize flow, accessibility, and overall productivity, ultimately streamlining their operations and enhancing their bottom line.
OSHA rack load capacity requirements
OSHA requires Load Application and Rack Configuration (LARC) drawings; however, many warehouse operators don’t have them on hand. North American guidelines and standards require that pallet rack owners display the load capacity limits of their racking systems and have up-to-date drawings available to health and safety officials when they visit.
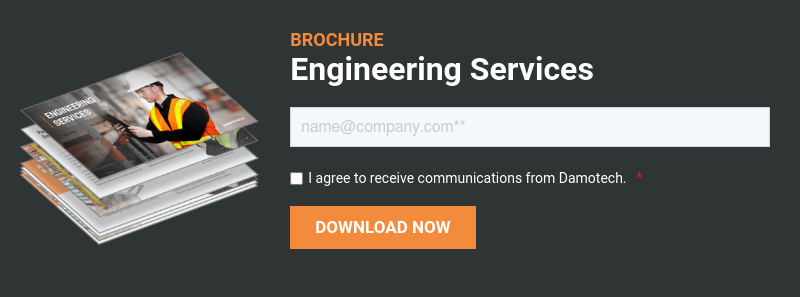
Why are rack load capacities limits required?
Industrial pallet racks are optimized steel structures designed to maximize the amount of storage area by stacking goods on multiple levels. Most rack components are made by cold-forming sheet metal less than 1/8 inch (3 mm) thick into a desired shape or form. Consequently, knowing how much weight they can support is imperative to avoid overloading them.
How much weight can pallet racking hold
A typical pallet rack compartment or cell can hold two pallets, each weighing 2,000 lbs on a pair of beams, for a total of 4,000 lbs. To put this weight into perspective, it is similar to storing a Ford F150 pickup truck at every beam level. Now imagine having a warehouse filled to the roof with such goods. Understanding the relationship between what is stored and how much can be stored in the racks is imperative. How should one know if the racking system can hold the load? This is where the pallet rack weight capacity, or LARCs, come in handy. Forklift drivers MUST know the weight capacity of each pallet position before loading them with the merchandise.
Different rack configurations mean different pallet weight capacities
Pallet racking load limits are limited by either the beams or the upright frames. It all depends on which part has the lowest load rating. For conventional systems, each upright frame bears half the loads carried on each attached beam pair. The cumulated beam loads are the vertical loads applied to the upright frame.
The illustration below (Figure 1) shows an altered racking system where the second upright from the left is overloaded, limiting the load on either side. For instance, the upright frame capacity is 24,000 lbs, the beams’ capacity is 5,000 lbs, and it is possible to store two pallets per cell (no beams are overloaded).
Figure 1. Understanding overloading of warehouse racking
Refer to the load capacity drawings (LARCs) for the safe use of pallet racks
Since pallet racks are manufactured for adjustability and easy assembly, some warehouse operators and owners may think that an existing pallet rack can be reconfigured without consequence to load capacity, for instance, by moving beam levels to accommodate new storage needs. However, such changes in beam level are not without consequences, as they may directly impact pallet racking load limits.
If rack beam levels are changed, added, or removed, that new configuration needs to be certified by a qualified engineer, documented with the LARC drawings, and kept on hand for reference.
Rack load capacity labels or plaques
Warehouse staff, including forklift drivers, need clear and easily accessible information regarding the weight capacity of racking systems. One effective method to communicate this information is by utilizing load capacity labels or plaques. Placing labels on the first beam elevation, positioned at eye level, offers optimal visibility and ensures that staff can easily reference the weight load capacity of the rack system. Load capacity labels placed on each bay are the most commonly used method to display this crucial information. In cases where the rack design remains consistent throughout the warehouse, rack load capacity plaques can be strategically positioned at the end of aisles and in tunnels to provide comprehensive guidance to personnel navigating the facility.
Key takeaway on pallet rack weight capacities and rack safety
Pallet rack load capacities and associated LARCs are indispensable tools for warehouse managers seeking to create safe, efficient, and organized storage environments. By prioritizing load capacity information and utilizing LARCs, managers can ensure the well-being of their workforce, protect valuable inventory, and optimize space utilization. Ultimately, this commitment to safety and efficiency translates into increased productivity and reduced costs, making pallet rack load capacities and LARCs a critical aspect of successful warehouse management.