A health and safety manager ensures employees are safe at work and that storage systems, such as pallet racks, are safe for workers.
Pallet racking is commonly used in warehouses, distribution centers, and manufacturing facilities for efficiently storing goods. However, they can become a serious safety hazard for employees and the warehouse if improperly used or maintained correctly.
Here are some key things to consider for pallet rack safety in warehouse environments:
1- Design and Load Capacity
Warehouse racking systems store heavy loads and must be designed to withstand the weight and stress placed upon them over time. As such, an engineer with expertise in designing structures capable of handling impressive loads should plan warehouse rack pallets.
Without proper planning and design, warehouse racks could fail, causing damage to stored goods and posing a risk to workers. An engineer can also ensure that the design of warehouse racks meets all relevant safety standards and regulations.
2- Installation
To prevent pallet rack collapses, it’s important to install the racking correctly.
Pallet racks must be installed according to the manufacturer’s instructions. It includes ensuring that the racking is level, plumb, and anchored to the floor, beams are secured, and uprights are correctly braced.
3- Maintenance
Proper maintenance is critical to ensuring the safety and longevity of pallet racking.
The health and safety officer should create a plan for regular cleaning and maintaining the racks. It includes removing debris, tightening loose bolts or hardware, and replacing missing parts.
Such a plan should be reviewed and updated regularly, as periodic maintenance is critical to ensure that racking remains in good condition and is safe to use.
4- Inspection
Pallet rack inspections are important for warehouse safety management. It is essential to conduct routine inspections since there are no alternative methods to assess the situation truly. Regular assessments can identify signs of rust, damage, or wear to the pallet rack, such as bent or cracked beams, uprights, or loose connections.
Establishing guidelines and procedures for inspections and conducting them regularly and thoroughly is essential. The primary concern regarding pallet racking safety is the potential for collapse. A collapse can occur if the racking is not installed correctly, overloaded, or not appropriately maintained.
Qualified inspectors should perform these inspections to identify potential hazards and safety issues. They must be familiar with OSHA regulations and industry standards and have the necessary training and experience.
After inspections, any findings should be documented. Appropriate action should be taken to address any identified issues, make repairs, implement safety measures, or provide employee training.
5- Loading and Stacking
Proper loading and stacking of pallet racks are essential for maintaining stability and preventing collapse or failure.
The weight of goods stored on storage racks should be, at most, their maximum load capacity, as specified by the manufacturer’s guidelines, which can vary depending on the rack type and materials stored.
The health and safety manager should understand the proper loading and stacking techniques for pallet racks to guarantee they are secured and will not fall over. Pallet racks should be loaded to distribute their weight evenly across beams to prevent instability.
Guidelines should also be followed for storing different materials on pallet racks, such as storing flammable materials in appropriate locations.
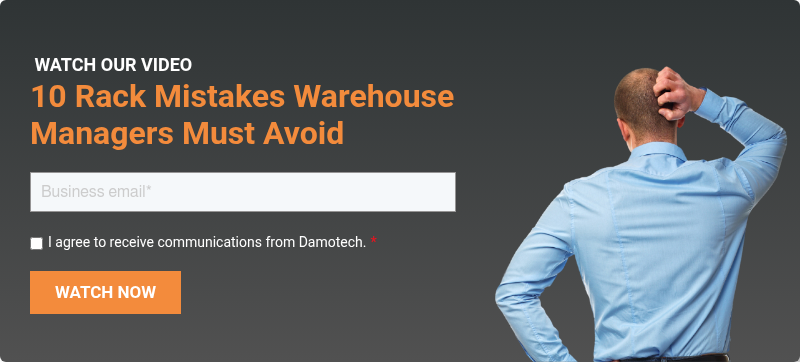
6- Clear Aisles
Adequately spaced racks with clear aisles are important to allow enough room for employees to move around and safely access the stored materials.
The aisle widths are determined based on the type of equipment utilized. According to OSHA, the width of aisles should be at least 4 feet or 3 feet wider than the largest equipment to ensure safe movement.
Establishing guidelines and procedures for clearing aisles and training employees to identify and report hazards can help prevent accidents and injuries. Any items in the aisles should be removed and returned to their proper storage location. Spills and leaks should also be immediately cleaned.
To guarantee the safety of the warehouse, monitor aisles regularly to identify hazards before they become a problem. Verify that aisles are marked, well-lit, and wide enough. This way, forklift operators can easily navigate the aisles, and employees can be aware of the traffic flow to prevent collisions.
7- Safety Signage
Safety signage is essential for pallet rack safety, such as compliance signs, danger warning signs, hazard warning signs, and material handling signs.
As a health and safety manager, you must identify the safety signs most relevant to your warehouse and determine where to place them. Ensure they are easily visible and legible and placed in a location easily accessible, such as near the pallet racks.
Safety signage should also be consistent in design and messaging. Always use the same colors, symbols, and wording so employees can easily recognize and understand the information.
You should also regularly inspect and maintain the signage to ensure that it is in good condition and that the information is still accurate. It includes checking for signs of wear or damage and replacing any signs that are no longer accurate.
ARE YOU TRAINED IN WAREHOUSE SAFETY?
HELP YOUR WORKERS UNDERSTAND THE POTENTIAL HAZARDS AND KNOW THE STEPS TO TAKE WHEN DAMAGE OCCURS.
8- Training
The health and safety manager must ensure that all staff who work with or around pallet racks receive appropriate training on safely using and maintaining the racks. The training should cover load capacity, proper loading and unloading techniques, and recognizing and addressing potential hazards.
Warehouse workers should also be familiar with safety procedures and protocols for working in the warehouse to prevent accidents.
9- Safety devices
As a health and safety manager, knowing about safety devices is important. For example, pallet stoppers help limit damage in case of accidental impact, safety bars prevent products from dropping between beams, and netting systems catch falling items or debris.
Column protectors are widely used to shield rack columns from damage and extend their lifespan. In addition, installing building column protectors can safeguard columns from collisions with forklifts or other vehicles, preventing costly repairs and downtime.
Integrating protection products can enhance the overall safety of the warehouse and safeguard employees against potential hazards.
10- Record Keeping
It is essential to keep accurate records to meet safety requirements. Keeping detailed records on pallet rack safety enables tracking rack condition and maintenance, incidents, near misses, or accidents. These records can identify trends and potential issues, validate that racks are adequately maintained and repaired promptly, and implement appropriate safety measures to prevent similar incidents.
The health and safety manager should also keep records of employee training on pallet racking systems, including the training date, the participant’s name, and any required additional training. This way, all employees can be adequately trained and, if necessary, retrained in a timely manner.
11- Emergency Procedures
Establishing a comprehensive plan for emergencies, such as a rack collapse or failure, is necessary. Employees should be trained on the types of emergencies that can occur, how to recognize an emergency, and how to respond appropriately.
Regular drills and simulations that cover all emergency plan elements, including emergency equipment and first aid, should be conducted.
A designated response team should also be responsible for managing the situation and ensuring the safety of employees. This team should be trained and equipped to handle the specific type of emergency most likely to occur.
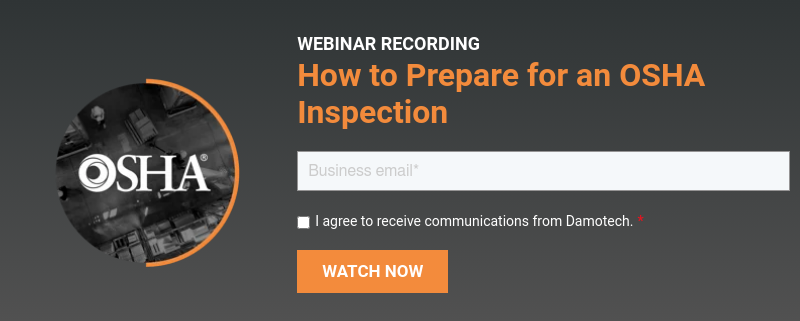
12- OSHA Regulations
The Occupational Safety and Health Administration (OSHA) has specific regulations related to the safe use of pallet racks that health and safety managers must understand for warehouse environments.
OSHA standards include regular inspections and maintenance of pallet racks, ensuring that rack systems are correctly loaded, not damaged, and easily accessible without obstacles and that employees receive safety training. Employers should maintain accurate and detailed records of inspections, maintenance, and any incidents or accidents in the warehouse.
Following OSHA regulations guarantees the safety of employees and the warehouse and avoids fines and penalties.
The 12 Things Every Health & Safety Manager Should Know About Rack Safety
Health and safety managers must understand the risks and best practices of pallet rack safety to ensure a safe warehouse.
They can enhance their company’s performance by following safety guidelines and implementing a rack safety program. This program should include regular inspections, employee training, and compliance with regulations.
Seeking expert guidance from rack safety professionals can also help them maintain a safe working environment by providing best practices, ongoing maintenance, or support during an incident.
In conclusion, prioritizing pallet rack safety is essential to ensure employees’ safety and the warehouse’s success.