With the invention of the first forklift truck back in 1915, skids – the early form of wooden pallets– were adapted to more modern machines. Improvements in the design soon followed with the first four-way pallet model created during World War 2 (Figure 2). The demand for this pallet increased rapidly because the need for effective transport of weapons was a priority. Years after, a variety of pallets with different shapes and materials were invented, such as disposable, heat-treated, plastic, corrugated cardboard, and metal pallets.
Today, choosing the right type of pallet can be a difficult task as several factors have to be taken into consideration. For instance, a pallet’s material, size, weight capacity, as well as the storage and retrieval systems used can make the process of handling pallets within the warehouse smoother and more effective. Below, you will find the most common types of wood and plastic pallets with their available size(s), load capacity and benefits. Innovative solutions of the future will also be explored.
Two-Way Vs. Four-Way Pallets
![]() |
Figure 1. Two-way entry pallet. |
Two-way pallets, such as stringer pallets (Figure 1), allow only front and rear fork entrance. Their design can restrict stacking and maneuvering activities in trailers and warehouses, as they need to be placed in a specific orientation for the forklift to be used and extra maneuvering time and care is required. The full utilization of the warehouse or facility space is limited. Nonetheless, these pallets are often considered more economical than four-way pallets and provide great strength and durability.
![]() |
Figure 2. Four-way entry pallet. |
Four-way pallets, such as block pallets (Figure 2) can be used with pallet jacks and forklifts. They allow fork entrance from all four sides, which greatly facilitates the maneuvering and handling, as well as optimizes the use of space. They are typically used for heavy loads that cannot be moved on two-way pallets. However, they are more expensive and sometimes less durable because the four sides of the pallets are used, increasing the possibility of damage.
Wood Vs. Plastic Pallets
Wood pallets are mostly used for general manufacturing, e-commerce, retail, export, and logistics and they are affordable ($5 to $25 each), recyclable, biodegradable, and repairable at a low cost. However, they harbor pathogens and other bacteria, especially in cooler environments that support bacterial growth due to moisture. They cannot be cleaned easily and have nails and screws that make them less safe in the handling of goods. Furthermore, they need to be replaced more frequently than their plastic counterparts, lasting only three to five years.
As for plastic pallets, these are used in all industries, especially in manufacturing, consumer durable, chemical, and pharmaceutical industries. They can be used in both dry and cool environments as they do not absorb moisture and will not allow microbes or bacteria to grow. They are easy to clean, recyclable, and they do not have screws or nails. They are lighter and have a longer lifespan than wood pallets - often more than 10 years. Yet, they have some disadvantages such as a higher initial cost ($10 to $100), they are difficult to repair, and they are not biodegradable.
Pallets Vs. Racks
The shape and size of pallets used in a warehouse will help determine the type of racks to be used. For example, the depth of pallets will certainly impact the depth of the racks because a three-inch overhang beyond the beams should be respected both for safety and for forklift accessibility. Moreover, the number of pallets to be place on the racks and their dimension will provide the total distance between the uprights, and ultimately the total span and the number of racking systems in the warehouse. Also, the horizontal and the vertical distance between rack beams can be calculated based on a combination of pallet width and depth with the load height.
The pallet type will help decide the right racking system to be used based on pallet design, maximum permissible unit load, and maximum total load per bay. For instance, two-way pallets can be used in drive-in, trolley push-back, and pallet racks, but cannot be placed in gravity and roller push-back systems. Two-way pallets also carry less load than 4-way pallets. Therefore, choosing the right type, dimensions and load capacity of the pallets will facilitate the warehouse operations and management of inventory, organize the warehouse space and logistics, and improve overall safety.
Pallet Specifications
The following tables show typical size, load capacity and general specifications containing pros and cons for wood and plastic pallets. Use it to evaluate your options in figuring out which type of pallet to use for your specific application.
Wood Pallets |
Specifications |
Recycled |
|
New |
|
Block |
|
Plastic Pallets |
Specifications |
Export |
|
Nestable |
|
Rackable |
|
Stackable |
|
Pallet Innovation
RFID Tags
![]() |
![]() |
Figure 3. Stick or staple RFID tag. | Figure 4. Hard RFID tags. |
One of the modern innovations in the world of pallets is the addition of an active radio frequency identification tag (RFID), which uses electromagnetic fields to track a pallet’s location within the warehouse. This helps to prevent theft or loss and will notify management or security about any unscheduled movement. In addition, this RFID tag improves the process of handling goods, increases the overall life span and longevity of the pallets, and reduces the cost and time for check-in and check-out as pallets enter and leave the warehouse. There are two common types: stick or staple tags (Figure 3) and hard tags (Figure 4).
Smart Pallets
![]() |
Figure 5. Smart pallets. |
There are “smart” pallets (Figure 5) that exist today which are equipped with a unique identifier such as a QR code or RFID tag and they have a Bluetooth hub attached underneath that enables the measurement of accelerations and movements, temperatures, and weights without the need of a person taking the measurements. This can be done through internet connectivity where live information about the pallets is uploaded automatically to a cloud-based software and shared with everyone in the supply chain or within the warehouse. This allows users to get beneficial operational data at regular intervals to optimize their logistics and improve the overall cost, coordination, and efficiency of the warehouse. They are considered as superior strength pallets that combine the best characteristics of both wooden and plastic pallets. They are more durable and lighter than the standard wood and plastic pallets which is economical in transportation energy. They are equipped with a ten-year service life battery.
Takeaways
Pallets are an essential part of many industries, warehouses, or trades, and choosing the right type of wood or plastic pallets depends on different factors such as size, weight capacity, equipment compatibility, material, price, environment and sustainability. As shown above, every type of pallet has its own advantages and disadvantages. It is ultimately up to the users to decide what will work best based on their needs and operations. Despite pallets having gone through many improvements and enhancements throughout the years, new innovations and ideas are still being introduced continuously to optimize their design. Implementing new technologies is important to keep up with the fast-growing industries in which pallets hold a pivotal role.
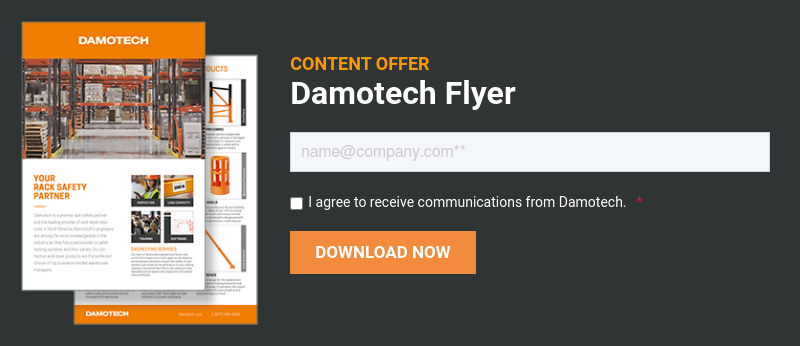