Creating a culture of safety in a warehouse environment is essential for the well-being of employees, the efficiency of operations, and the overall success of the business. Warehouses are busy, dynamic environments with a high risk of accidents and injuries.
According to the U.S. Bureau of Labor Statistics, the warehousing and storage industry reported 22,600 injuries and illnesses in 2020, with a rate of 4.0 cases per 100 full-time workers. By prioritizing safety, companies can reduce incidents, increase productivity, and create a more positive workplace culture. This comprehensive article will explore the steps and strategies needed to build and maintain a safety culture in your warehouse.
What is Safety Culture in the Workplace?
Workplace safety culture refers to the shared values, beliefs, practices, and attitudes within an organization regarding the importance of safety. It encompasses how safety is managed in the workplace and how safety is prioritized by employees at all levels, from top management to frontline workers.
What Does Safety Culture Mean and Why Is It Important?
A culture of safety is a workplace environment where safety is a core value, and everyone is committed to maintaining a safe and healthy workplace. Safety protocols in a warehouse are not just rules to follow but are integrated into everyday operations and decision-making processes. A strong safety culture can lead to:
- Reduced Workplace Injuries: Fewer accidents and injuries mean less downtime, lower medical costs, and a healthier workforce.
- Increased Productivity: Safe workplaces are more efficient as employees can perform their tasks without fear of injury.
- Higher Employee Morale: Employees who feel safe and valued are likelier to be engaged and satisfied with their jobs.
- Compliance with Regulations: Adhering to safety standards helps avoid legal penalties and maintains the company’s reputation.
How Do Organizations Develop a Culture of Safety? 7 Steps Proven Strategies
1. Leadership Commitment
The foundation of a safety culture starts with leadership. Management must demonstrate a genuine commitment to safety by:
- Leading by Example: Executives and managers should consistently follow safety protocols and wear appropriate Personal Protective Equipment (PPE).
- Allocating Resources: Ensure sufficient resources (monetary and effort) are dedicated to safety programs, including training, equipment, and personnel.
- Communicating the Importance of Safety: Regularly communicate the significance of safety in meetings, newsletters, and other internal communications.
A proactive leadership approach involves not only adhering to safety standards but also actively participating in safety training sessions and audits. Leaders should be visible in their commitment to safety by being present on the warehouse floor, engaging with employees, and addressing safety concerns promptly.
2. Employee Involvement
Engaging employees at all levels is crucial to creating a successful safety culture. This can be achieved by:
- Forming Safety Committees: Create a cross-functional team of employees who meet regularly to discuss safety issues and initiatives.
- Encouraging Reporting: Develop a non-punitive system for employees to report hazards, near misses, and unsafe behaviors.
- Involving Employees in Decision-Making: Include employees in discussions about new safety measures and solicit their feedback.
Employees should feel empowered to voice their safety concerns without fear of retribution. This can be facilitated through anonymous reporting systems, regular safety meetings, and open-door policies where employees can approach supervisors with concerns.
3. Comprehensive Training Programs
Training is essential to ensure employees recognize safety risks, understand safety procedures, and know how to apply them. Effective training programs should include:
- Onboarding Training: Introduce new hires to the company’s safety culture, policies, and procedures from day one.
- Regular Refresher Courses: Conduct periodic training sessions to keep safety knowledge current.
- Specific Skill Training: Provide training tailored to specific tasks, such as forklift operation, material handling, and emergency response.
Training should be interactive and engaging, utilizing various methods such as hands-on demonstrations, video tutorials, and scenario-based exercises. Assessments should be conducted to ensure that employees understand and can apply the training effectively.
4. Establishing Clear Safety Policies and Procedures
Clear, well-documented policies and procedures are the backbone of a safety culture. These should be:
- Accessible: Ensure that all employees can easily access safety policies and procedures.
- Comprehensive: Cover all aspects of warehouse operations, including equipment use, hazard identification, and emergency protocols.
- Regularly Updated: Keep policies and procedures up to date with the latest safety standards and practices.
Policies should be written in clear, understandable language and readily available in multiple formats, such as printed handbooks, posters, and online resources. They should also be reviewed and updated regularly to incorporate new or updated safety regulations and industry best practices.
5. Conducting Regular Safety Audits and Inspections
Regular audits and inspections help identify potential hazards and ensure compliance with safety policies. Effective audits should:
- Be Systematic: Follow a consistent process to thoroughly inspect all areas of the warehouse.
- Involve Employees: Engage employees in the audit process to gain their insights and foster a sense of ownership.
- Result in Actionable Reports: Provide clear, actionable recommendations for addressing identified hazards.
Safety audits should be scheduled at regular intervals and include internal and external auditors to provide a comprehensive and standardized assessment. Follow-up actions should be tracked and documented to resolve identified issues promptly.
6. Promoting a Safety-First Mindset
Fostering a safety-first mindset involves:
- Recognizing and Rewarding Safe Behavior: Implement programs to acknowledge and reward employees committed to safety.
- Promoting Open Communication: Encourage employees to discuss safety concerns and suggestions.
- Integrating Safety into Daily Operations: Make safety a regular part of team meetings, shift handovers, and daily routines.
Creating a culture where safety is prioritized in every aspect of work can be achieved by integrating safety reminders into daily briefings, displaying safety posters and signs throughout the warehouse, and making safety a key performance indicator in employee evaluations. Additionally, employees can be rewarded for their commitment, idea submission, reporting inadequate behavior, or identifying safety risks or issues.
7. Pallet Rack Safety
Pallet racks are essential for maximizing warehouse space but pose significant safety risks if improperly maintained. Key aspects of pallet rack safety include:
- Regular Inspections: Conduct frequent inspections to identify issues, damage, or wear.
- Routine Maintenance: Ensure that the insight gained from the inspections is transferred into maintenance projects to repair or replace damaged components. Well-maintained racks are essential to prevent them from collapsing.
- Rack Protection: Install rack protection units to prevent racks from being damaged in the first place.
- Proper Loading: Ensure that load capacities are up to date, loads are evenly distributed, and the weight capacity of the racks is not exceeded.
- Employee Training: Train employees on rack safety procedures and proper loading and unloading techniques, to avoid overloading and uneven stacking.
- Clear Signage: Post signs indicating the load capacity and proper use of pallet racks.
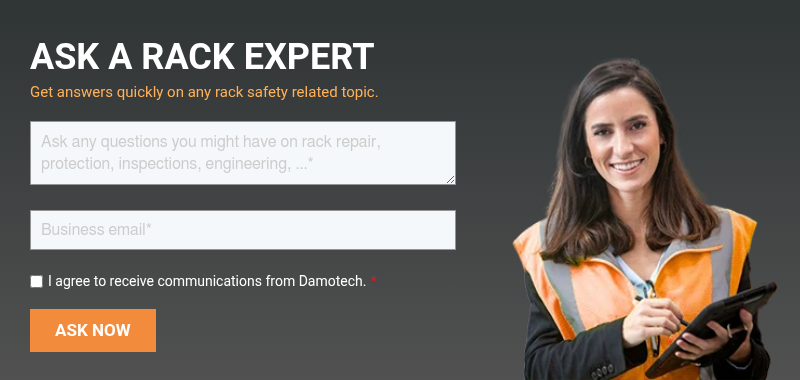
In Conclusion: Safety Culture in the Workplace Starts with Commitment
Building a strong safety culture in your warehouse is an ongoing process that requires continuous effort and commitment from everyone involved. By prioritizing safety, you can create a work environment where employees feel valued and protected, ultimately leading to a more productive and successful operation.
Remember, safety doesn’t happen by accident. Partner with Damotech for expert guidance on warehouse safety solutions and ensuring the structural integrity of your racking systems. We offer comprehensive services, including rack inspections, rack repair and maintenance, warehouse safety training, and safety products.
Top Questions and Answers on Creating a Safety Culture in Warehouses
Q1: What is warehouse safety?
A1: Warehouse safety encompasses all practices and procedures designed to prevent accidents and injuries in a warehouse environment. This includes everything from proper training and equipment use to maintaining a clean and organized workspace. Effective warehouse safety practices ensure that employees can perform their duties without risk of harm.
Q2: What are the key elements of a strong safety culture?
A2: Key elements include leadership commitment, employee involvement, comprehensive training, clear policies and procedures, regular audits and inspections, and a safety-first mindset. Each element is crucial in creating an environment where safety is a top priority, and all employees feel responsible for maintaining a safe workplace.
Q3: How can management demonstrate a commitment to safety?
A3: Management can lead by example, allocate resources for safety initiatives, and consistently communicate the importance of safety to all employees. This includes actively participating in safety training, addressing safety concerns promptly, and recognizing employees contributing to a safer workplace.
Q4: What role do employees play in building a safety culture?
A4: Employees play a crucial role by participating in safety committees, reporting hazards, providing feedback, and adhering to safety policies and procedures. Their active involvement ensures that safety measures are practical and effective, and their input can lead to continuous improvement in safety practices.
Q5: How often should safety training be conducted?
A5: Safety training should be conducted during onboarding, with regular refresher courses and specific skill training as needed. This ensures all employees know the latest safety procedures and can perform their tasks safely. Regular training helps maintain a high level of safety awareness and competency.
Q6: What should be included in a safety audit?
A6: A safety audit should systematically inspect all warehouse areas, involve employees, and provide actionable recommendations for improving safety. It should cover aspects such as equipment condition, emergency preparedness, hazard identification, and compliance with safety regulations.
Q7: How can a safety-first mindset be promoted?
A7: A safety-first mindset can be promoted by recognizing safe behavior, encouraging open communication, and integrating safety into daily operations. This can be achieved through safety recognition programs, regular safety briefings, and making safety a core value of the company.
Q8: What is the impact of neglecting warehouse safety?
A8: Neglecting warehouse safety can lead to increased accidents and injuries, higher medical costs, legal penalties, and decreased employee morale and productivity. It can also damage the company’s reputation and result in financial losses due to downtime and compensation claims.
Q9: What are the main PPEs for warehouse workers?
A9: The main Personal Protective Equipment (PPE) for warehouse workers includes hard hats, safety goggles, gloves, high-visibility vests, steel-toed boots, and hearing protection. These PPEs are essential for protecting workers from hazards, such as falling objects, chemical splashes, cuts, and loud noises.
Q10: What are the main regulations that need to be observed?
A10: The main regulations that must be observed in warehouse safety include OSHA (Occupational Safety and Health Administration) standards, ANSI (American National Standards Institute) guidelines, RMI MH16.1 requirements, and local safety regulations. These regulations cover various safety aspects, including equipment use, hazard communication, emergency procedures, and PPE requirements.
Q11: How can rack damage be addressed?
A11: Rack damage can be addressed through timely repair and replacement. Regular inspections should identify any damage, which should be promptly repaired to prevent further issues. If the damage is beyond repair, replacing the affected components is crucial to maintaining the integrity and safety of the racking system.
Q12: What needs protection in a warehouse?
A12: In a warehouse, several elements require protection, including:
- Racks: Protection units and guards should be installed to prevent damage from forklifts and other equipment. Engineered rack repair kits also act as a protection against future impact.
- Employees: Proper PPE, training, and safety protocols should be in place to protect workers from injuries.
- Inventory: Secure storage and handling practices should be implemented to protect goods from damage. Netting and other devices may protect merchandise from falling.
- Equipment: Fences and other guarding products should be installed to protect machinery and equipment from damage by forklifts or other heavy vehicle equipment.
- Building Structural Elements: Columns, walls, and other structural elements should be safeguarded against impacts and potential damage. Bollards, fences, and pallet stoppers can be used to prevent damage.
Q13: How often should racks be inspected?
A13: Racks should be regularly inspected, ideally monthly, with more thorough inspections conducted quarterly or annually. The frequency of inspections may vary depending on the usage and load conditions, but regular checks are essential to ensure the safety and integrity of the racking system.
Online Resources for Warehouse Safety
1. Occupational Safety and Health Administration (OSHA)—OSHA Warehouse Safety
2. National Institute for Occupational Safety and Health (NIOSH)—NIOSH Workplace Safety and Health Topics
3. American National Standards Institute (ANSI)—ANSI Safety Standards
4. Warehouse Education and Research Council (WERC)—WERC Safety Resources
5. Material Handling Industry (MHI)—MHI Safety Resources
6. National Safety Council (NSC)—NSC Workplace Safety
7. Institute of Hazardous Materials Management (IHMM)—IHMM Safety Resources
8. Safety and Health Magazine—Safety and Health Magazine
9. The International Warehouse Logistics Association (IWLA)—IWLA Safety Resources
10. Damotech Blog—Damotech Rack Safety Blog
These resources provide valuable information on various aspects of warehouse safety, including best practices, regulatory updates, training materials, and safety guidelines.
- Top 12 Largest Warehouses in North America (Size, Tech & Safety)
- Top 100 Warehouse Safety Quotes for Toolbox Talks, Posters & Meetings
- Costco’s Supply Chain Strategy: Decoding Its Warehousing Approach
- Minimum Distances Between Pallets, Rack Systems & Building Structures
- IKEA Warehouses: Efficient Warehousing and Distribution Strategies