Warehouses have been operated conventionally for a long time. Labor workers have had to physically handle products from the moment they are received until they are shipped out. Over decades, automation has slowly made its way into the material handling industry. In the 1960s, a Japanese material handling equipment company named Daifuku cut costs by developing the first automated storage and retrieval system (AS/RS) in Japan. Another example is the introduction of the robotic arm in the U.S. during the same time period. Some people were afraid that such robots would take over their jobs. With that in mind, the robotic arm made its debut by being marketed as the solution for dangerous tasks such as welding and lifting heavy loads. Today, new technologies continue to make their way into the warehouse industry and the operational limitations that come with manual labor are being challenged – making way for new innovations.
In the U.S., roughly 70% of warehouses are still manually operated whereas the other 30% are either semi-automated or fully-automated. Just as the manufacturing and transportation industries have adopted new technologies and grown with the times, the material-handling industry can potentially follow a similar path. However, change is not always easy. And automation does come with its own set of drawbacks. Employees need to be consistently trained to operate equipment – which can also be hard to adapt (as it can only follow hard-coded programming). It also requires routine maintenance causing occasional downtime. One of the biggest drawbacks of automation can be the high initial investment required. This financial barrier can discourage companies from incorporating these technologies into their warehouse.
The reason for introducing such technologies into a warehouse should be to improve quality and consistency, increase safety, improve workers’ experience, accelerate production, and to reduce costs. Technology can achieve this by various means including upgrading workflow efficiency, minimizing damages, maximizing utilization of floor space, increasing pick throughput, increasing inventory control, and reducing physically strenuous activities. In this article, you will see how automation, robotics, and augmented reality are being tested or used in the material handling industry.
Robotic Arms Used in Manufacturing
Different robotic arm types are available in various industries and workplace applications today. For instance, in production lines, robotic arms are widely used for assembly, painting, and welding. While in warehousing, robotic arms are great tools to assist with picking, sorting, packing, and palletizing more accurately. They help by reducing errors, minimizing repetitive and demanding activities, speed up order fulfillment, and more. For example, some beverage companies use robotic arms to stack boxes of their products on pallets. This allows for a quick and consistent stacking of pallets all while minimizing labor intensive work for their employees. Furthermore, smaller robotic arms are being designed to potentially do the same tasks as an order picker. However, some of these newer products are still being tested.
Using Augmented Reality to Train Employees
![]() |
Figure 2. Smart glasses. |
![]() |
Figure 3. Smart glasses wearer's view. |
With 70% of warehouses being operated conventionally, one of the most intensive and expensive tasks is order fulfillment. Employee turnover rate in a warehouse is typically 25%. The problem of continuously having to train new employees could be sped up with smart glasses (augmented reality) as they provide an intuitive learning experience resulting in a faster integration of the employee. Smart glasses extract the information from the warehouse management system (WMS) and display it on the heads-up display as seen in Figure 3. They can display a map to allow users to find the optimal route to their destination within the warehouse by specifying the exact aisle and bay to find their required product. When picking, the glasses can project an image to ensure the correct product is picked and will even prompt an error on the heads-up display if the wrong product is scanned. These glasses enable workers to locate, scan, sort, and move inventory without needing a handheld scanner or referencing hard-copy forms. In some cases, such a product has yielded a 15% efficiency increase during the picking process.
Automating Warehouse Inventory Management with Drones
![]() |
Figure 4. A drone scanning barcodes in a warehouse. |
Drones have been gaining popularity over the last decade and have various commercial applications such as delivery of products. Some of the biggest obstacles for such an application is unstable weather, strict aviation regulations (which also vary from one area to another) and the limits of the drone itself to carry heavy loads. However, indoor drone applications provide mostly stable weather conditions, a controlled/stable environment, less restrictive regulations, and several interesting applications which can reduce hazardous tasks for employees and save time.
Firstly, drones can provide assistance in some form of surveillance. The use of indoor drones has increased; they can reach high, hard to see places easily to have a better view of pallet positioning, clearances, and some information concerning the loads that are stored, which are normally not visible from the ground. However, their uses are still somewhat limited and unpractical as they have a short battery life and have limited accessibility within the rack. Secondly, drones provide warehouses with a robotic solution for stock taking (inventory). They can provide live feedback and be integrated with warehouse management systems (WMS). Manual stock taking is a slow, labor intensive task which can also be achieved via drones. Drones can patrol aisles scanning barcodes, QR codes and text to gather all the required product information in the warehouse.
In some cases, drones have even been proven to be 20x times faster than conventional methods. It should be noted that drones are limited to single deep racks as they would have a hard time scanning anything beyond the first product. Therefore, everything that would require scanning must not be only visible and intact (not damaged), but also be facing outwards so that the drone may be able to read it. Any pallets with their labels facing the rear of the system will not be taken into account by the drone.
Pallet Handling with Automated Guided Vehicles (AGVs)
![]() |
Figure 5. AGVs at the charge station. |
![]() |
Figure 6. AGVs and their pre-determined paths. |
AGVs are load carriers that travel along the floor following a pre-determined path with no operator or driver. These vehicles navigate using several guidance technologies such as floor mounted magnetic tape or bars, lasers, and optical sensors. When adequately equipped with sensors, AGVs can detect other moving objects whether it be a forklift or a person and stop accordingly. They can also be programmed to avoid stopping near critical pathways such as emergency exits and entrances. They are well suited for repetitive movement of materials over a distance. They are often used to handle raw materials, products, pallets, and containers. Using AGVs for trailer loading is becoming increasingly popular as well.
One of the most popular uses of AGVs is pallet handling. An example would be Amazon’s storage and retrieval system which utilizes AGVs. They have AGVs picking up portable storage units with the required products and bringing them to the picker. This allows for the picker to stand still and wait for all items to be delivered to them, saving time, and reducing unnecessary movement for employees.
Autonomous Mobile Robots (AMRs)
![]() |
Figure 7. Driverless forklift from Toyota (AMR). |
How do they differ from AGVs? AMRs are very similar but more flexible as they do not require a path to follow. They have many more sensors allowing them to understand their environment and react to any sudden changes. Unlike AGVs, they navigate dynamically using a map by finding the quickest and most efficient path to their destination. Driverless forklifts are an example of AMRs. They can pick up pallets without supervision and determine the shortest/most ideal route to their destination where the load needs to be dropped off.
Automated Storage and Retrieval Systems (ASRS)
![]() |
Figure 8. Shuttles. |
Automated storage and retrieval systems do exactly what their name implies, they automatically store products and retrieve them as requested. In other words, they are like gigantic vending machines. They eliminate the employees’ need for search and travel, saving them time. They also reduce damages to the products and chances of human error (misplaced inventory). According to some ASRS companies, their systems are compact, saving up to 85% of floor space in some cases, resulting in a picking accuracy of 99.9%, allowing for greater inventory control and throughput while minimizing labor costs. ASRS can be used in a wide variety of applications such as storage of parts in a manufacturing process, order picking, and securing expensive tools, dyes and molds. An ASRS system can be scaled to the end user’s exact needs. There are a couple of different types and configurations of ASRS. Some deliver an entire tray of products, others individual bins, while some deliver the required product only to the operator.
Focus on the Present Yet Keep One Eye on the Future
If automation is not yet possible for you, this does not mean that you cannot improve the efficiency of your warehouse activities and make them safer in more traditional ways. For example, one of the reasons for introducing automation in the warehouse is to increase safety. Working with a knowledgeable rack safety solutions provider can give you the support needed to not only make your warehouse safer, but also make your operations more cost-efficient. Safety cannot wait for the next high-tech trend to surface. Warehouse managers have certain responsibilities – even if they are toying with the idea of purchasing the next big thing in warehouse automation, augmented reality, and robotics. It would be wise to focus on the present, improve what you can today, and always keep one eye on the future. In many cases, companies must weigh the pros and cons to automation and see if it is a transition they can sustain long-term. In other words, taking the leap towards automation cannot and should not be done on a whim.
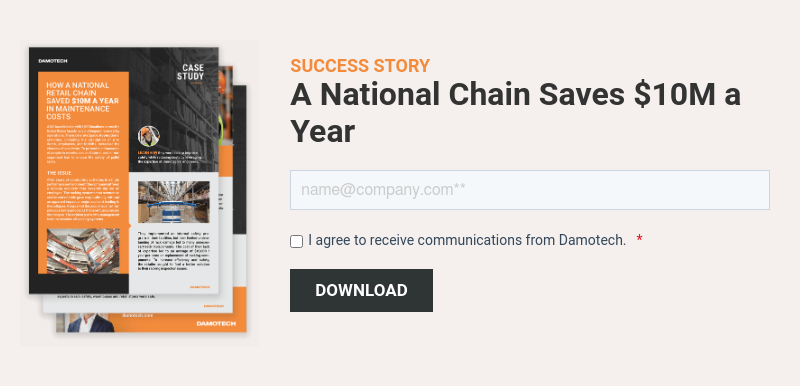