Imagine the phone call: a worker has been severely injured—or worse—on your watch. In the moments that follow, you’re not just faced with the shock and sadness of a life forever changed; you’re also left grappling with the haunting question: *Could this have been prevented?*
The unsettling truth is that many warehouse injuries, including fatal ones, result from hazards that could have been mitigated with the right precautions. As a warehouse executive, the safety of your workforce isn’t just a line item on a budget or a compliance checkbox—it’s a profound responsibility. When someone gets hurt or killed, it’s not just about fines or downtime; it’s about a father, a mother, or a friend who might never come home again.
The costs of warehouse injuries extend far beyond dollars—they reverberate through families and communities. But here’s the good news: with the right strategies, tools, and commitment, many of these tragedies are entirely preventable.
What are the most common warehouse injuries? How do you prevent them?
1. Slips, Trips, and Falls
With an injury rate of 22.6 per 10,000 workers, those 55 and over in transportation and warehousing face the highest risk—most often losing 14 days to sprains, strains, and tears.
— U.S. Bureau of Labor Statistics (BLS), 2021–2022
Slips, trips, and falls are some of the most common and preventable warehouse injuries. These incidents often result from wet or uneven surfaces, cluttered walkways, or inadequate lighting. The injuries range from minor bruises to severe fractures and head injuries.
Real-life examples of warehouse slips, trips, and falls
1. In 2021, a worker at a distribution center in Fort Worth, Texas, slipped on an oil spill and fell, resulting in a severe back injury. The worker required surgery and was out of work for six months. The company faced a lawsuit and settled for $300,000 in damages in addition to increased insurance premiums. The incident brought negative media attention, highlighting the company’s failure to maintain a safe work environment.
2. An employee suffered multiple fractures after falling from a ladder in an Atlanta warehouse. The ladder was found to be faulty, and the incident led to a $70,000 OSHA fine. The worker spent three months in rehabilitation, costing the company nearly $50,000 in workers’ compensation and lost productivity. This incident resulted in a review of all safety equipment across their warehouses.
How to prevent slips, trips, and falls
1. Anti-Slip Flooring and Mats
Anti-slip flooring materials and mats provide additional traction on wet or oily surfaces, significantly reducing the risk of slips.
Cost: Ranges from $10 to $50 per square foot.
Effectiveness: Can reduce slip incidents by up to 60%.
Best Used In: Entryways, loading docks, and areas where liquids are frequently handled.
2. LiDAR and Vision Systems
LiDAR (Light Detection and Ranging) and vision systems use laser and camera technology to detect real-time obstacles and hazards. These systems are typically mounted on machinery or positioned in key areas rather than being worn by the worker. The system scans the environment continuously, creating a detailed map of the surroundings.
If it detects a potential hazard—such as an object in a walkway, a wet floor, or an uneven surface—it can alert the worker through visual signals on a screen, auditory warnings, or even automated actions like slowing down machinery.
Cost: Typically $2,000 to $5,000 per system.
Effectiveness: Reduces trip-related incidents by up to 25%.
Best Used In: Walkways, corridors, and warehouse sections with frequent foot traffic.
3. Safety Harnesses
When working on ladders or elevated platforms, safety harnesses are generally more standard and effective than safety nets. Harnesses, often attached to fixed anchor points, prevent falls by arresting the worker’s descent if they slip or lose balance.
Cost: Typically, harnesses cost $150 to $300, and anchor systems range from $500 to $1,500.
Effectiveness: Safety harnesses can prevent up to 95% of serious injuries from falls when used correctly.
Best Used In: Areas where workers perform tasks at heights, such as mezzanines, high racks, or while using ladders.
4. Proper Footwear
Requiring all employees to wear anti-slip footwear can significantly reduce slip incidents.
Cost: High-quality safety footwear typically ranges from $50 to $150 per pair.
Effectiveness:No specific data is available, but it is generally recommended in high-risk areas.
5. Training Protocols and Checklists
A comprehensive training program that includes regular refresher courses on slip, trip, and fall prevention is essential. This should be combined with daily checklists to ensure walkways are clear and spills are promptly addressed.
Cost: Training programs typically range from $300 to $1,000 per participant.
Effectiveness: Regular training can reduce incidents by 30%.
Best Used In: All areas, with particular emphasis on high-traffic zones.
6. Regular Maintenance and Housekeeping
Maintaining a clean and organized warehouse is critical to preventing trips and falls. This includes regular inspections to identify hazards like spills, clutter, and damaged flooring.
Cost: In-house maintenance programs can vary widely, but outsourcing cleaning services typically costs $0.15 to $0.50 per square foot.
Effectiveness: Proper housekeeping can reduce trip and fall incidents by up to 40%.
Best Used In: High-traffic areas, walkways, and storage zones.
Top 5 Daily Warehouse Checklist:
1. Inspect floor surfaces for spills or wet areas.
2. Clear all walkways of obstacles.
3. Verify proper lighting in work areas.
4. Check safety harnesses and anchor points for integrity.
5. Ensure employees are wearing approved anti-slip footwear.
OSHA provides comprehensive regulations on walking-working surfaces. In Canada, the CCOHS provides similar guidelines for preventing slips, trips, and falls.
2. Vehicle Accident Injuries
Vehicle-related injuries, particularly involving forklifts, are a leading cause of death and serious injury in warehouses. These accidents typically occur when vehicles collide with pedestrians, tip over, or when operators lose control of the vehicle.
The most common types of vehicle-related injuries include being struck by a vehicle, caught between a vehicle and another object, or crushed under an overturned vehicle.
Real-Life Examples of Warehouse Incidents
1. In 2019, a warehouse worker in Robbinsville, New Jersey, was struck and killed by a forklift. The incident led to a major OSHA investigation, resulting in significant fines and mandatory safety reforms across the company’s warehousing network. The worker’s death highlighted the dangers of vehicle operation in congested areas of the warehouse. The company faced over $28,000 in fines, while the incident resulted in 5 days of shutdown operations at the facility, costing them millions in lost productivity and bad PR.
2. A forklift accident at a warehouse in Cincinnati, Ohio, resulted in the death of an employee when the vehicle overturned. The investigation revealed that the worker had not been wearing a seatbelt, which contributed to the fatality. The incident led to a $90,000 fine for the company and a significant increase in their insurance premiums. The warehouse manager was terminated, and the incident prompted a review and enhancement of safety protocols across all the company’s facilities in North America.
How to prevent vehicle accident injuries
1. Proximity Sensors and LiDAR Systems
These systems use laser-based technology to detect objects or people in the vicinity of a moving vehicle. When an obstacle is detected, the system alerts the operator with visual or auditory signals, or automatically slows or stops the vehicle.
Cost: Approximately $1,500 to $3,000 per vehicle.
Effectiveness: Studies have shown a 30% reduction in vehicle-related accidents in warehouses using these systems.
Best Used In: High-traffic areas and loading docks where visibility is limited.
2. Backup Cameras
Backup cameras provide operators with a clear view of the area behind the vehicle, significantly reducing blind spots. These cameras are particularly effective in preventing accidents when reversing.
Cost: Ranges from $500 to $1,200 per unit.
Effectiveness: Reduces rear-collision incidents by up to 25%.
Best Used In: Areas where vehicles frequently reverse, such as loading docks and narrow aisles.
3. Automated Guided Vehicles (AGVs)
AGVs are self-operating vehicles that navigate through the warehouse using pre-programmed paths or sensors, reducing the risk of human error.
Cost: AGVs can cost between $20,000 and $150,000 depending on the complexity of the system.
Effectiveness: Virtually eliminates vehicle-pedestrian collisions in areas where AGVs are used exclusively.
Best Used In: High-risk areas that can be isolated for AGV use, such as heavy-load transport routes.
4. Speed Limiters and Controlled Zones
Speed limiters cap the maximum speed at which a vehicle can travel within certain zones, while controlled zones use physical barriers to restrict vehicle access.
Cost: Speed limiters cost around $200 per vehicle, and the infrastructure needed to implement controlled zones varies.
Effectiveness: Can reduce the incidence of high-speed collisions by up to 50%.
Best Used In: High-traffic zones and pedestrian-heavy areas.
5. Physical Barriers
Bollards, safety gates, and fences create physical separations between vehicles and pedestrians, preventing accidental collisions.
Cost: Installing physical barriers can range from $1,000 to $10,000 per barrier, depending on the type and size.
Effectiveness: Reduces collision risks by creating clear boundaries.
Best Used In: Pedestrian walkways, entrances, and loading dock areas.
6. Training Protocols and Checklists
Implementing comprehensive training for vehicle operators, including daily pre-operation checklists, can drastically reduce accidents.
Cost: Operator training programs vary widely but typically range from $500 to $2,000 per operator.
Effectiveness: Regular training and adherence to checklists can reduce vehicle-related accidents by up to 40%.
Best Used In: All areas where vehicles are operated.
Top 5 Daily Warehouse Checklist:
1. Inspect proximity sensors and backup cameras.
2. Check for obstructions in vehicle paths.
3. Verify speed limiter settings.
4. Examine physical barriers.
5. Perform pre-operation vehicle checks.
OSHA mandates specific safety measures for powered industrial trucks, including training, operation, and inspection protocols. In Canada, the equivalent standards are governed by the Canadian Centre for Occupational Health and Safety (CCOHS), which provides detailed guidelines on forklift safety.
3. Musculoskeletal Disorders
Musculoskeletal disorders (MSDs) result from repetitive motion, heavy lifting, and poor ergonomics. Common MSDs include back strains, carpal tunnel syndrome, and tendonitis.
Real-Life Examples of Warehouse Incidents
1. A warehouse worker developed severe back pain after months of lifting heavy boxes without ergonomic support. The worker filed a workers’ compensation claim and was awarded $15,000, but the company faced criticism for not providing adequate ergonomic solutions. That facility had one of the highest rates of MSDs, leading to bad PR and an OSHA investigation.
2. A worker developed carpal tunnel syndrome after repeatedly scanning and sorting packages for extended hours. The injury resulted in surgery and six months of rehabilitation, during which the worker was unable to return to work. The company faced $50,000 in workers’ compensation costs and increased insurance premiums.
How to prevent MSDs
1. Ergonomic Workstations
Adjustable workstations allow workers to maintain proper posture, reducing the risk of back and joint injuries.
Cost: $500 to $2,500 per workstation.
Effectiveness: Can reduce the occurrence of MSDs by 40%.
Best Used In: Packing, sorting, and assembly areas.
2. Wearable Lift-Assist Technology
Devices such as exoskeletons or posture-correcting wearables provide support during lifting and can alert workers to improper movements.
Cost: $1,000 to $5,000 per device.
Effectiveness: Reduces back strain by up to 30%.
Best Used In: Areas involving heavy lifting or repetitive tasks.
3. Automated Lifting Systems
Automated systems, such as robotic arms, handle heavy loads, minimizing the need for manual lifting.
Cost: $20,000 to $100,000 depending on complexity.
Effectiveness: Virtually eliminates manual lifting injuries.
Best Used In: High-volume packing and distribution areas.
4. Task Rotation
Rotating workers between different tasks reduces repetitive strain injuries by giving muscles and joints time to recover.
Cost: Minimal; involves scheduling adjustments.
Effectiveness: Reduces RSIs by up to 20%.
Best Used In: Workstations where repetitive tasks are common.
5. Regular Breaks
Encouraging workers to take regular breaks reduces the risk of overexertion and repetitive strain.
Cost: Minimal.
Effectiveness: No specific data is available, but it is recommended by occupational health experts.
6. Training Protocols and Checklists
Comprehensive training on proper lifting techniques and ergonomic practices, combined with daily checklists to monitor workstation setups, is essential.
Cost: $300 to $1,000 per participant.
Effectiveness: Reduces MSDs by 30%.
Best Used In: All workstations, especially those involving manual handling.
Top 5 Daily Warehouse Checklist:
1. Assess workstation ergonomics.
2. Monitor task rotation compliance.
3. Inspect lifting equipment.
4. Verify break schedules.
5. Evaluate wearable devices.
OSHA provides detailed guidelines on ergonomic practices to prevent musculoskeletal disorders. These include requirements for proper workstation setup, lifting techniques, and employee training. In Canada, the CCOHS offers similar guidelines for workplace ergonomics.
4. Struck by Falling Objects
Struck-by injuries are common in warehouses where items are stored on high racks or moved using forklifts. Falling objects can lead to severe injuries, including fractures, head trauma, and even fatalities. Additionally, flying objects from tasks like cutting or grinding can result in serious eye injuries.
Real-Life Examples of Warehouse Incidents
1. An employee was struck by a pallet that fell from a high rack, causing severe head trauma. The worker survived but required months of rehabilitation. The incident led to a $75,000 fine from OSHA, a lawsuit settlement of $500,000, and a temporary shutdown of the warehouse for safety inspections.
2. A forklift operator accidentally knocked over a stack of pallets, striking and killing a fellow worker. The incident resulted in a $125,000 fine and a major overhaul of the company’s racking safety protocols. The warehouse manager was dismissed, and the company faced substantial bad PR.
How to prevent struck-by accidents
1. Safety Nets on Racking Systems
Safety nets installed along racking systems prevent items from falling, reducing the risk of injuries.
Cost: $1,000 to $5,000 depending on area coverage.
Effectiveness: Can prevent up to 90% of injuries from falling items.
Best Used In: High-density storage areas.
2. Secure Storage Practices
Properly securing items on shelves and racks ensures they do not shift or fall.
Cost: Training and materials range from $500 to $2,000.
Effectiveness: Reduces incidents by 30%.
Best Used In: All racking areas.
3. Overhead Guards on Forklifts
Overhead guards protect operators from falling objects when transporting materials.
Cost: $500 to $1,500 per guard.
Effectiveness: Reduces the risk of injury by 25%.
Best Used In: Areas with high racking and frequent forklift traffic.
4. Hard Hats and Eye Protection
OSHA mandates that workers in environments with risks of falling or flying objects wear hard hats and safety goggles or face shields. Hard hats must meet ANSI Z89.1 standards, and eye protection must meet ANSI Z87.1 standards.
Cost: Hard hats typically range from $15 to $50, while safety goggles range from $10 to $30 per pair.
Effectiveness: Wearing hard hats and eye protection can reduce head and eye injuries by up to 70%.
Best Used In: Areas with overhead hazards, tasks involving cutting, grinding, or any work where flying debris is possible.
5. Regular Safety Audits
Routine inspections identify and mitigate potential hazards from improperly stored items.
Cost: $1,000 to $5,000 depending on warehouse size.
Effectiveness: Reduces risk by 20%.
Best Used In: High-traffic and high-storage areas.
6. Training Protocols and Checklists
Implement comprehensive training that focuses on the proper stacking of materials, the use of personal protective equipment (PPE), and the safe operation of forklifts. Pair this with daily checklists for managers to ensure that storage areas are secure and that any overhead or flying object hazards are identified and addressed.
Cost: $300 to $1,000 per participant.
Effectiveness: Training and regular safety checks can reduce the risk of struck-by incidents by 30%.
Best Used In: All storage and high-traffic areas, with a focus on regions with elevated racks or where flying debris is possible.
Top 5 Daily Warehouse Checklist:
1. Secure racking systems.
2. Inspect safety nets.
3. Test overhead guards on forklifts.
4. Ensure hard hats and eye protection are worn.
5. Check for loose items on racks.
OSHA mandates the use of head and eye protection in environments with potential struck-by hazards. In Canada, the CCOHS provides similar guidelines.
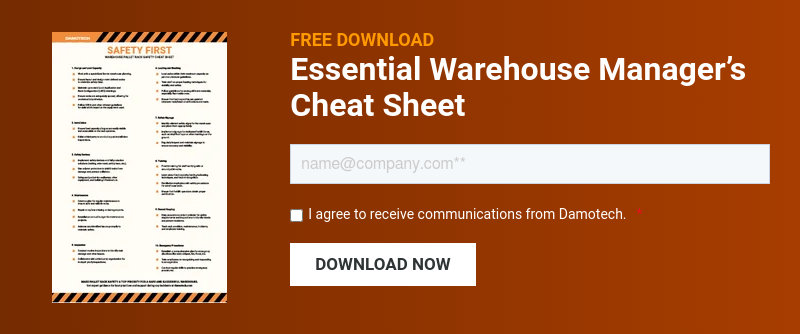
Conclusion: Reducing Warehouse Injuries—A Critical Priority for Safety and Success
Warehouse injuries are a critical issue that impacts the well-being of workers and carries significant financial and reputational risks for businesses. From vehicle accident injuries to slips, trips, falls, and exposure to hazardous materials, the dangers in a warehouse are numerous, but they are also preventable.
Implementing the prevention strategies outlined above can significantly reduce the risk of injury, ensure compliance with safety regulations, and maintain a productive and safe working environment.
Investing in safety is not just about avoiding fines or reducing insurance premiums—it’s about protecting lives and ensuring that every employee returns home safely at the end of the day.
The data shows that with the right mix of technology, training, and proactive safety measures, many of the most common warehouse injuries can be prevented. The path forward is clear: prioritize safety, invest in prevention, and create a culture where safety is a fundamental part of the operation. The cost of inaction is simply too high.