If you walk through any warehouse, chances are you have witnessed impact damage on pallet racking systems. Over 85% of rack damage occurs in the bottom 24 inches, but it can also occur at greater heights as forklift drivers are loading and unloading pallets. To ensure the safety of all workers, these damages must be addressed in a timely manner because even the most harmless-looking dent on your pallet racking can potentially contribute to a system collapse. As an owner of steel storage systems, you are responsible for keeping your warehouse employees safe. Ultimately, the decision must be made to either repair the damaged racking component or replace it with OEM (Original Equipment Manufacturer) parts. Below we have debunked 10 common rack repair myths to help you make an informed decision, and ultimately do what is best for your facility.
Myth 1: Rack repair is more expensive than rack replacement.
Depending on the style of racking, rack repair can often be a fraction of the cost of rack replacement, and with minimal to no unload of racks required, the downtime in your warehouse operations is short. In comparison, the cost of downtime involved in rack replacement is significant. Besides the cost of the new racking component, there is also the cost of getting your maintenance crew to unload and dismantle the damaged rack. And while you wait several weeks for the new rack to be manufactured and delivered, operations in and around the area of which the damage occurred may need to be shut down, which in and of itself has an incurred cost (especially if you are a third-party logistics warehouse or 3PL). To learn more about how much you can save by choosing rack repair, download our Brace Repair Vs. Upright Replacement or our Rack Column Repair Vs. Upright Replacement infographics.
Myth 2: Repair kits are only meant to repair front rack columns.
Rack repair kits can repair front and back rack columns, as well as rack braces. They are also ideal for the end of warehouse aisles, which are generally more prone to high traffic and damage from forklift collisions. Rack repair kits are usually bolted in place and anchored to the floor. One of the advantages of rack repair is that each kit can be custom-built, meaning it can fit onto any style of rack, from any manufacturer. These kits can be fitted to a rack with a single damaged pallet rack column or one that needs both front and rear columns repaired at once. There is also a rack repair kit that can be bolted onto cantilevered racking systems. This variety of rack repair options makes it seamless for rack owners to find the kit that will meet their specific needs.
![]() |
Figure 1. Three different types of rack repair solutions. |
Myth 3: Rack manufacturers do not approve of rack repair.
Rack Manufacturers Institute (RMI), the governing body of the storage rack industry, approves and endorses rack repair, as long as the engineering of the repair meets the RMI/ANSI MH 16.1 specification. This code states that the repair must restore the rack to at least its original design capacity – and this should be confirmed by a rack safety professional. RMI’s Guidelines for the Assessment and Repair of Replacement of Damaged Rack (Version 2.0) state that “it can be economical or advantageous to remove the damaged section of an upright and to replace it with a component from a pre-engineered rack repair kit.” One example of rack repair being the best solution is when a rack gets damaged, and the original design documentation is not found. In this case, one cannot simply order a new rack upright from the same manufacturer and interchanging different styles of racks is highly recommended against by RMI. Therefore, an engineer specialized in rack safety should assess the situation, make the required calculations, and ultimately recommend a pre-engineered rack repair solution.
Myth 4: Rack repair requires the rack to be completely unloaded, causing a halt in warehouse operations.
When a repair kit is being installed, a type of rack supporting device is used to allow for very minimal unloading. This tool is secured to the rack while the repair is being performed, supporting the weight of the load. Thanks to this device, the installation process of a repair unit is safe and generally done in under an hour. This process is non-disruptive to your operations. In contrast, replacing a damaged upright requires the removal of each beam on both sides of the upright. Prior to this, the area should be cordoned off as complete unloading of the rack is necessary to allow for its dismantling.
![]() |
Figure 2. A specially designed device is used to support the load while the repair kit is being installed. |
Myth 5: Rack repair means longer downtime.
Rack repair kits can be manufactured in about four weeks. Ordering OEM replacement takes 8-12 weeks on average. Kits can also be ordered proactively and stored in your warehouse. For example, brace repair kits do not take up a lot of space and since these kits can be self-installed, is it wise to pre-order these so that the next time brace damage is spotted, it can be resolved quickly.
Myth 6: A single damaged brace will not impact the structural integrity and load capacity of a racking system.
One damaged brace, depending on the severity of the dent or cut, could considerably degrade the structural integrity of the entire racking system. Therefore, if you spot any missing or detached braces, these need immediate attention. If you see cracked or broken welds in the braces, these need to be addressed as well. Several small damages on rack bracing can compound and weaken the structure. It is recommended to turn to a rack repair expert when in doubt.
Myth 7: Rack repair kits lower the overall rack load capacity.
Engineered rack repair kits are designed to respect the original configuration of the rack, as well as maintain the rack’s original load capacity. In other words, there is zero impact to how much weight you can load onto the same rack. The same is true for brace repair kits. Damotech’s DAMO BRACE is actually stronger than most braces that come on your original rack. Remember, knowing and displaying your pallet rack load capacity, as well as having load application and rack configuration (LARC) drawings on hand are both critical to the safe operation of your warehouse. If you are ever in doubt regarding your load capacity calculations, a rack safety expert should be consulted.
Myth 8: Rack repair kits need to be welded on.
Welding is not required at all. Rack repair kits are bolted on to your existing rack and anchored to the ground with high shearing capacity anchors. Even in a seismic area, for example, there are repair kits that will be adapted for that environment. Field welding in a warehouse is complicated and not recommended. It poses risks such as fire hazard. To learn more about why homemade repairs can be unsafe, read this article.
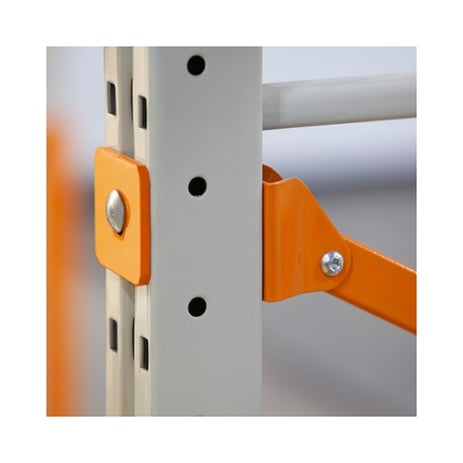
Figure 3. This brace repair kit is bolted (not welded) onto the rack column. |
Myth 9: Rack Repair kits are hard to install.
Most rack repairs can be installed from A to Z in under 30 mins by professional installers, depending on what rack component needs repairing. Some repair installations may require certified installers to do the job and others can be self-installed by following a few simple steps. For example, a brace repair can be installed by your maintenance crew within minutes. All repair products come with the necessary hardware and anchors.
Myth 10: Rack repair kits are not as robust (and therefore not as safe) as OEM parts.
Some engineered rack repair kits are stronger that OEM parts because they are built using components made of heavy gauge steel (such as hollow structural steel, or “HSS” tubing) to offer true impact resistance. They are also built to withstand the harshest of environments. Kits can also be galvanized to prevent rusting (for outdoors & freezers). Some rack repair kits are built so strong that they come with a lifetime warranty against impact, which cannot be said about OEM racks.
Rack Repair: A Sound Alternative to Rack Replacement
Debunking these common myths shows that rack repair is a safe and viable solution to rack damage in your warehouse. Not only does rack repair make more sense economically, but it can also save you downtime as repair kits can generally be manufactured much faster than OEM parts. Repair kits can also be stored in your facility, ready to be installed instantly when damage occurs. The most important point to keep in mind is that you should not perform a repair without consulting a rack repair expert first. It is important to find a reliable and experienced rack safety partner who can guide you in finding the most suitable and efficient rack safety solutions to not only repair damage to your racking systems caused by forklifts, but to also help you improve the overall safety of your warehouse. Purchasing from a ProGMA member ensures you are getting products that are engineered to hold up to the industry's highest standards.
At Damotech, our extensive line of pallet rack repair kits is so indestructible; every unit comes with a 10-year manufacturer’s warranty. Some repair kits, like Damotech’s DAMO PRO, come with a lifetime manufacturer’s warranty, as they are guaranteed to protect against future impact. Every kit is designed according to your warehouse needs. The DAMO PRO is our repair kit that started it all; designed and patented for the front and/or back legs of a frame in a pallet rack system. Our DAMO FLEX is our versatile modular rack repair kit solution. Its modularity comes from the fact that the braces on are not welded to the repair unit, allowing installers to measure, and cut them on-site. Our DAMO BRACE can repair damaged braces, at any angle and length.
Our rack safety solutions providers also offer on-site rack damage assessment services, performed by experienced rack safety experts. These professionals will share helpful advice on how to ensure your racking systems will stand up permanently to the repeated impacts from forklifts. To better manage your rack inspections, the Damotech Platform can help you access crucial rack data from virtually anywhere! Accessible via the cloud, you can track racking issues easily with the real-time dashboard. Watch the demo to see how you can modernize the way you manage your rack inspections at your company!
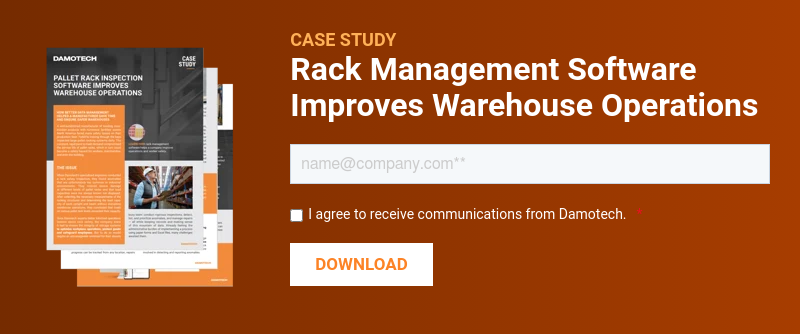
- Top 100 Warehouse Safety Quotes for Toolbox Talks, Posters & Meetings
- Top 12 Largest Warehouses in North America (Size, Tech & Safety)
- Costco’s Supply Chain Strategy: Decoding Its Warehousing Approach
- Minimum Distances Between Pallets, Rack Systems & Building Structures
- IKEA Warehouses: Efficient Warehousing and Distribution Strategies