Warehouses can be subjected to structural problems in their lifespan that can affect their operational, management, and safety procedures. These problems can be related to damaged structural building components of the warehouse such as the interior and the exterior walls, the columns, the foundation, the concrete slab, etc. One of the most common issues related to the concrete slab is the differential settlement that some warehouses may develop over time. If you’re wondering about concrete repair, sunken concrete, or are involved in building a warehouse, this article will be of help.
A differential settlement means the uneven settlement of the soil beneath the foundation of a structure that may lead to the “sinking” of different parts of the structure, which causes cracks and other structural problems.
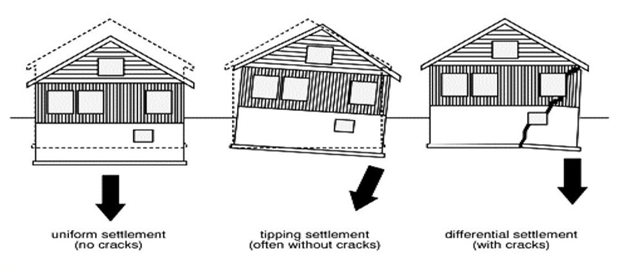
Figure 1: Types of settlement
Uneven concrete slab settlement can lead to some complications within the warehouse. It can affect the efficiency of mobile machinery operations and most certainly result in unstable and out-of-plumb equipment such as shelving and rack systems. Replacing the concrete slab or adding shims under the column baseplates to level the racks may sound like appealing solutions, but both come with difficulties. Both will cause operational problems for the warehouse and pouring a new concrete slab can be very expensive and time-consuming. This article will present two separate solutions to concrete slab settlement, giving an in-depth comparison and analysis.
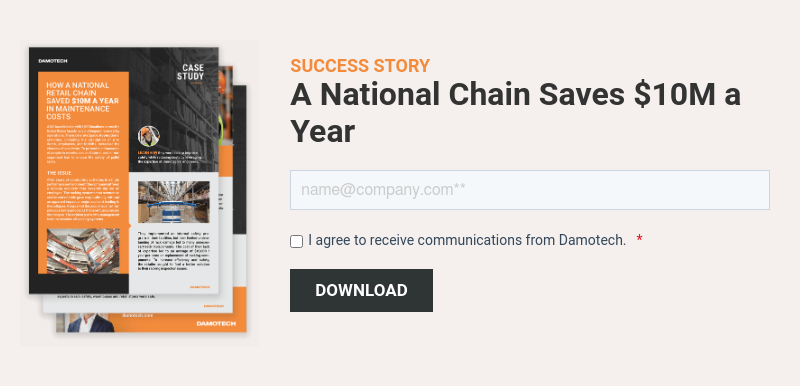
Why Does Differential Settlement Occur in Warehouses?
Differential settlement can happen due to a variety of factors, including inhomogeneous subsoil properties, non-uniform load patterns on the floor, poor-quality soil reports, and inadequate site preparation. Since the soil under the slab will ultimately be bearing the load throughout the facility’s lifetime, it is imperative that adequate preliminary soil testing is done. This will indicate if there are issues with the structural stability of the soil, and if so, what can be done to improve it. All these factors, and more, can influence the degree of the slab settlement and how critical the issue will be in the future.
In some cases, like in shipping/receiving areas of the warehouse, pallets may be constantly placed and even stacked on the floor. Due to large weights being placed in a concentrated area, it may be more susceptible to settle over its lifetime than the slab around it. Another common practice in some warehouses may be to push pallets directly across the floor using the lift truck. This method is used by drivers to save time by not having to stack pallets. However, this can damage the concrete slab, possibly resulting in an uneven settlement in the future. Keep this in mind when managing your pallet racking systems.
Sometimes even if all these steps are taken into consideration, and an experienced construction crew provides a flawless installation, other factors can still cause the concrete slab to settle. For instance, soil settlements or concrete creep – deformation of concrete due to long-term pressure or stress- are both time-dependent. Potential problems might arise after a period of 2 to 5 years after construction.
Settling Concrete Slab (Sinking Concrete Slabs) Solutions
Mudjacking
Mudjacking is the process of hydraulically pumping or injecting a mixture of water and high compression strength materials. These include pond sand, sandy loam, limestone, topsoil mixtures, or Portland cement inserted under the concrete slab to raise it back to its initial level.
The process consists of the following four steps:
- One or two-inch diameter holes are drilled directly into the concrete slab.
- The mudjacking mixture is prepared on-site and loaded into the portable pump.
- The mixture is pumped into the holes until the void beneath the concrete slab is filled. The slab is then leveled due to the pumping pressure.
- The drilled holes are filled by pouring a concrete mixture or epoxy.
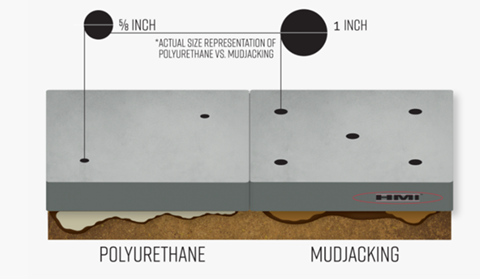
Expanding Structural Foam Leveling (Polyurethane Foam)
Like the concept of mudjacking, foam leveling injects a mixture into the drilled holes to lift the concrete slab. However, instead of cementitious grouts, polyurethane is used. Polyurethane is a two-part polymer (resin and activator) that results in a closed-cell polymer foam. This foam is formed when two separate liquids travel down the hoses and mix in the nozzle to create cells sealed from each other. Hence, the foam will not retain water or moisture, and it will not be subjected to erosion after being placed. It is challenging to measure how much polyurethane should be pumped underneath the slab and how much foam will expand. The process should be performed by a professional technician with years of experience in the field.
This process involves three steps:
- 3/8 or 5/8-inch diameter holes are drilled in the concrete slab at specific locations.
- Two parts of the polymer are pumped into the holes. The mix of the two liquids will create an expanding foam that will lift the concrete slab.
- The drilled holes are filled with a concrete mixture.
Mudjacking vs. Expanding Structural Foam Leveling (Polyurethane)
Advantages |
Disadvantages |
|
Mudjacking |
|
|
Polyurethane |
|
|
Takeaways
Having out-of-plumb racking systems in the warehouse due to uneven or settling concrete slab can cause safety concerns and lead to additional problems with material handling equipment within the warehouse. Therefore, instead of replacing the settling concrete slab or using pier systems to uplift it, which will be much more expensive and time-consuming, mudjacking and polyurethane are the two most common solutions used today to solve the settling concrete slab issue. They both follow a similar concept of uplifting the slab by injecting a mixture beneath the concrete, raising it back to its original level.
Mudjacking uses the pumping pressure of cementitious grout to raise the slab. On the other hand, polyurethane leveling relies on expanding the closed-cell foam to achieve the same results. It’s important to have experts in concrete leveling perform both solutions to have the desired slab flatness and levelness.
ReferencesFor a quick and durable repair, polyurethane leveling would be a good option, as it takes less than an hour for the concrete to cure, and once it is installed, it will be there permanently. Yet, mudjacking is cost-effective and environmentally friendly.
- https://www.a1concrete.com/what-is-poly-leveling-foam-concrete-leveling#process
- https://hmicompany.com/concrete-raising/polyurethane-concrete-raising/
- https://www.theconcretehero.com/2020/04/mudjacking-vs-polyurethane-foam-raising-which-is-right-for-you/
- https://usstn.com/blog/3-options-repair-sunken-concrete/
- https://www.geobear.co.uk/re-leveling/
Want expert advice to prevent and address warehouse problems due to your racking systems? More than half of the Fortune 500 trusts Damotech's rack repair and protection products and engineering services. From inspections to load capacity calculations, our experts can help.