While maximizing warehouse space is a concern for many businesses, some may be unable to afford a larger warehouse. Additionally, it’s worth noting that others may face the challenge of not having available warehouse space in their area, especially if they are in densely populated cities or areas with high real estate prices.
It can be a significant challenge, especially if your business is growing and you need more room to store inventory and other essential items. However, a few strategies can help you make the most of your current space.
How to maximize your warehouse space utilization
This article will discuss tips and tricks for warehouse space, including organizing inventory efficiently, optimizing storage, and more, regardless of budget or location constraints.
Whether you’re a small business owner or a large distribution center manager, these strategies can help you overcome the challenges of limited warehouse space and keep your operations running smoothly.
Organize your warehouse inventory
One of the most important things you can do to optimize your warehouse space utilization is to organize your merchandise. By keeping an accurate inventory of what you have, you’ll be able to find what you need more efficiently and make better use of the space you have. It also helps to ensure that your warehouse is organized and efficient.
1. Implement efficient inventory management
Keep a detailed inventory of all items stored in the warehouse to help identify those not being used and can be removed or sold. Keep track of inventory levels and rotate products to move older items to the front for quick turnover. It can help free up space and improve efficiency.
2. Group similar warehouse items together
Optimize your product placement by grouping similar items, such as all electronics in one area, all clothing in another, and so on. You can also arrange products based on their size, weight, and usage frequency. For example, group all small parts in one bin and all large parts in another.
Products you frequently use should be stored in easily accessible locations, while products used less regularly should be stored in less accessible areas. This will make it easier to find specific items and keep track of inventory levels.
3. Use labels
Clearly label each shelving unit with the items it contains (item name and code) so workers can easily find and retrieve them. This will make it easier to restock. Use color-coded labels to identify the type of item quickly. For example, use red tags for hazardous materials, yellow for fragile items, and green for general items.
4. Implement a FIFO system
Use a “first in, first out” system to ensure that older items are used or sold first before they expire or become obsolete. It can help prevent wasted space and ensure that goods are used efficiently. Keep older items separate to ensure you do not accidentally ship them out before newer items. It will help ensure that the FIFO system works correctly and that older articles are not wasted.
5. Establish a cycle counting program
A cycle counting program helps you keep track of your inventory by counting items in a specific area of your warehouse on a regular schedule. Determine the program’s goals (e.g., improving inventory accuracy, identifying discrepancies, reducing labor costs) and how often cycle counts will be conducted (based on item turnover, lead time, and importance).
6. Train your staff
Train your employees on handling inventory management, such as receiving and tracking inventory, conducting regular inventory counts, and identifying and reporting discrepancies.
Provide them with hands-on training opportunities, such as mock inventory counts or inventory tracking exercises, to give them experience managing inventory. Encourage open communication and reward good performance for encouraging accuracy and accountability.
Implement an effective warehouse storage system
Another strategy for freeing up space is implementing a storage system to store more items in less space.
A storage system specifically designed for your products and materials can ensure that your products are organized and easily accessible, helping maximize warehouse space utilization. Choose a storage system that is easy to use and maintain to improve efficiency and can quickly expand or modify as your needs change.
Remember to regularly review and reorganize the warehouse to ensure that items are stored in the most space-efficient way possible.
1. Optimize your warehouse layout
You should review and assess your warehouse layout to better use your space. It means organizing your warehouse to make the most of your available space. For example, you can use a U-shaped layout to keep items close to the loading docks or a linear structure to keep goods close to the shipping area.
2. Utilize vertical space in your warehouse
Many warehouses have high ceilings that are not utilized to their full potential. Vertical space can be utilized to gain more storage space in less floor space.
Create additional storage space by using mezzanine levels to double your warehouse space without expanding the building and stacking racks. You can also install shelving units on the walls and ceilings to store small parts, tools, and equipment.
High-density storage systems to maximize storage capacity
You can also maximize storage capacity by installing high-density storage systems, such as vertical carousels or lift modules, allowing you to store products at a higher level, freeing up floor space.
Pallet racks and shelving units
Pallet racks can help you maximize storage space as they utilize the full height of the warehouse. They are a popular and efficient way to store large quantities of items of different sizes and weights in a vertical configuration.
Additionally, you can configure the racking in various ways to optimize the use of the available space. For example, narrow aisle racking can reduce the width of aisles and increase storage capacity.
3. Invest in compact storage solutions
You can increase storage capacity without expanding the warehouse’s physical footprint.
Compact storage solutions are smaller than traditional storage units and can be placed in tight spaces, such as corners and narrow aisles, to maximize space. For example, depending on the needs of the warehouse, mobile shelving units can be moved together to create more space or used apart.
Containers and pallets to maximize the use of available space
Collapsible containers and folding pallets also allow for more efficient storage because, when not in use, they can be collapsed or folded to take up less space. Additionally, these containers and pallets can be stacked on each other when in use, allowing for more storage space or even downsizing to a smaller warehouse.
4. Use space-saving equipment
Compact equipment such as compact forklifts, hand trucks, pallet jacks, and electric stackers can help save warehouse space. These types of equipment are designed to take up less space than traditional equipment, making it easy to move items around the warehouse without cluttering the floor space. Also, by using space-saving equipment, you can store more items in less space.
5. Fill unused space in your warehouse
Unused spaces, such as attics and basements, can be converted into storage spaces. This is a great way to add extra storage space to a warehouse and free up space on the main floor. For example, you can store items you don’t frequently use, such as seasonal products or overstock.
You can use the basement or attic as a staging area for products waiting to be shipped or received. But if you plan to store items sensitive to temperature and humidity, consider adding climate control to keep them in optimal condition.
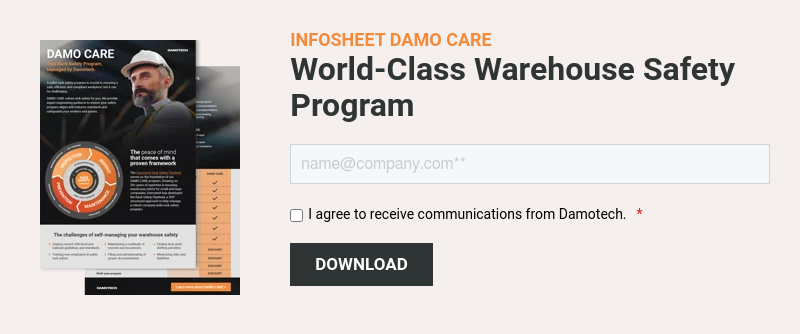
Automate warehouse operations
Warehouse automation can be a valuable tool for businesses looking to maximize their warehouse space. By using automation, you can free up space and improve your operations.
With advanced technology, such as automation systems, and inventory management software, businesses can streamline their operations and maximize their available space.
1. Implement automated warehouse management
Automating warehouse operations starts with implementing a warehouse management system (WMS) to manage orders, optimize picking and packing processes, and streamline processes.
You can also use warehouse management software to automate inventory management and optimize warehouse operations, such as tracking and reporting inventory levels and analyzing data to identify areas of improvement.
2. Allow real-time tracking
Barcode scanning and radio-frequency identification
This technology can help maximize warehouse space by improving inventory management and visibility. Both technologies can track inventory levels and reduce the risk of overstocking by providing up-to-date information on stock levels, location, and movement.
Enhance warehouse operations with inventory tracking
Barcode scanning technology is generally less expensive and easier to implement, but RFID offers more advanced features, such as real-time tracking and a longer read range.
Since barcodes do not automatically track in real time, you could continuously scan items and update their location information using fixed scanners at critical locations or mobile scanners that warehouse workers could carry as they move through the warehouse.
3. Implement automated storage equipment
Conveyor systems
Automated storage systems such as conveyor belts and robotic systems (like drones) can help save warehouse space. Storage conveyor systems can automatically move items from one location to another within your warehouse, reducing the need for manual handling and freeing up valuable floor space.
For example, you can use them to move items from storage to shipping areas or create multi-level storage systems, where products are stored on different levels and easily accessed by the conveyor. It allows more products to be stored in a smaller area, as the conveyor system can move products to and from different levels as needed.
Automated storage and retrieval systems
Additionally, you can use ASRS, such as robotic arms, to store and retrieve items more efficiently. Storage conveyors can automate storing and retrieving products, reducing the need for manual labor, and freeing up space that would otherwise be used for manual storage and retrieval.
4. Main points to consider for warehouse automation
Depending on the project’s scope, automating warehouse processes and systems can be expensive as it requires purchasing, installing, and maintaining specialized software or equipment. However, it can save labor costs, improve productivity, and reduce human error in the long run.
Gradual implementation of automation solutions
You can progressively implement some automation solutions to make costs more manageable rather than investing in a full-scale automation project. Other solutions, such as warehouse management software and barcode scanning systems, are relatively affordable and can be implemented with minimal upfront costs.
These solutions can also provide a significant return on investment by improving inventory accuracy, reducing labor costs, and increasing efficiency. You should weigh the potential benefits against the costs and determine if automation is the right choice for you.
ARE YOU THINKING OF CHANGING YOUR PALLET RACK CONFIGURATION? CONSULT A RACK SPECIALIST. OUR EXPERT WILL ASSESS THE CHANGES YOU NEED TO MAKE AND HOW TO IMPLEMENT THEM SAFELY AND EFFICIENTLY.
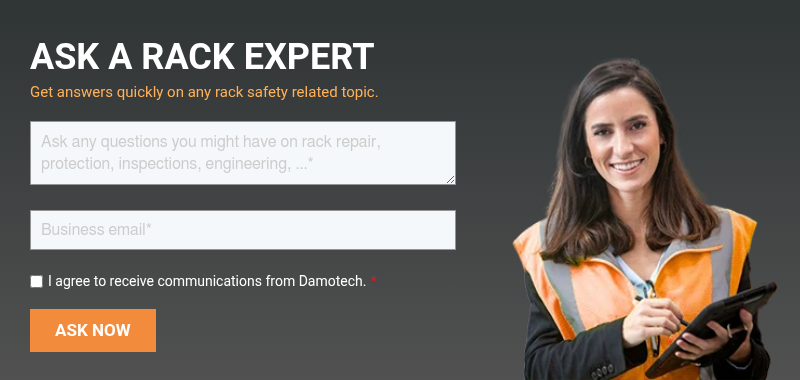
KEY Takeaways for Optimizing Your Warehouse Space
Warehouse space is a valuable commodity, and making the most of every square foot is essential. With the increasing demand for goods and services, warehouses can become cluttered and disorganized, making it challenging to utilize the available space effectively.
While expanding the warehouse may seem like a solution, many ways exist to optimize the current space and keep operations running smoothly. With creativity and smart planning, you can optimize your warehouse space and maximize your resources.
Maximizing Your Warehouse Space Utilization: Assessing Your Needs and Adopting Strategies
By assessing your specific needs and adopting strategies, you can improve your operations and take your business to the next level. These strategies include implementing a storage system, organizing inventory, or utilizing technology. Find the right balance of these solutions that will work best for your warehouse.
Remember to consult a rack expert or engineer before implementing any warehouse modifications, such as installing new racks, changing the racking system layout, or adjusting the height of specific beams. Their expertise and experience can help you achieve your goals and ensure your warehouse space utilization is optimized safely.