Pallet racks are very flexible and versatile structures. They allow beams to be placed at various heights to accommodate all kinds of materials and goods. However, a warehouse owner or manager must be cautious when modifying an existing pallet rack system since one slight change can significantly change its capacity and structural integrity.
All pallet rack owners must have their racks’ load application and rack configuration (LARC) drawings on hand. These documents outline the maximum allowable weight that can be supported on each beam level for specific configurations. If a configuration changes, the LARCs are no longer valid, and the pallet rack capacity has most likely been altered.
This blog post discusses four common rack modifications that can affect your pallet racks more than you may think.
1. Moving or removing beams on racking
With the way beams seamlessly clip in and out of their compatible uprights, it is very tempting to move them around, add/remove them to accommodate different loads, or increase storage space. However, such changes will most likely impact the rack’s load capacity. The example below demonstrates how the capacity of your rack could be drastically reduced by removing just one beam level to make room for larger loads.
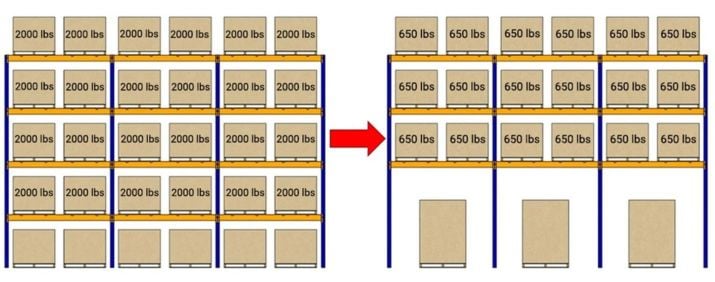
For this reason, rack modifications should always be done under the supervision of a professional engineer. Every time a change is made, updated load capacities should be calculated and displayed to maintain safe operations. Failure to do so could lead to extremely dangerous situations, like a rack collapse (see videos).
2. Replacing pallet rack components
The most common mistake we see in warehousing is replacing a single damaged upright with another one without considering if it is exactly the same. It may look the same, but the steel gauge (thickness) and brace configuration are often overlooked. This greatly impacts the rack load capacity and creates a weak spot in your system, which is now prone to collapse.
When beam components are damaged, the simplest solution is to replace them. In such cases, verifying that the replaced beam is identical to the previously used one or the one specified in your LARCs is critical. Never install a beam that is incompatible with the uprights being used. Assembling incompatible beams and uprights could greatly reduce the lateral stability of your racking system. Furthermore, any dislodging caused by inadequate connections between beams and uprights could lead to rack safety concerns.
Installing a replacement beam that differs in shape, size, or thickness from the original part will also affect the rack's load capacity.
Because of these possible issues, replacing any component with identical replacement parts is essential. When in doubt, it is a good idea to contact your original equipment manufacturer (OEM) or a rack expert to confirm the compatibility of your pallet rack components.
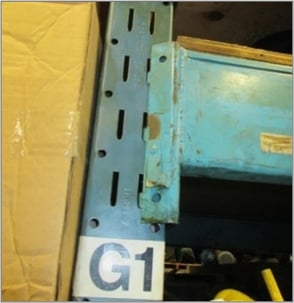
Figure 2. Incompatible components
3. Adding rack upright extensions
Multiple warehouse owners have added upright extensions at the top to accommodate an additional beam level.
Don’t think about doing that in your warehouse unless you first consult with the OEM or a professional rack design engineer! And don’t load the racks until you’ve received signed and stamped updated LARCs. Not following these guidelines could lead to overloading of the existing rack, change their seismic behavior, void the OEM’s warranty, leaving you with unsafe racks and no recourse.
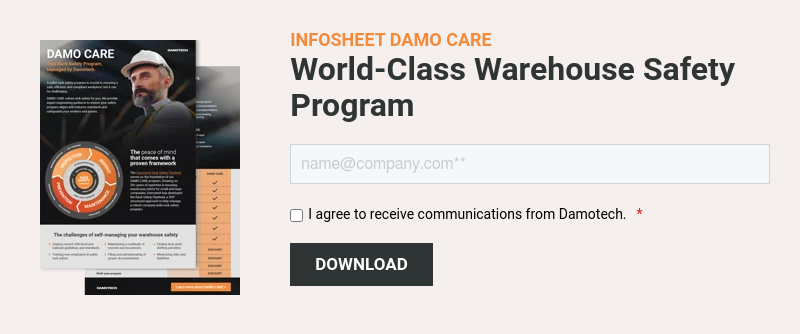
4. Repairing damaged rack components
All approaches to rack repair are not created equal. Racks are highly optimized structures that need all their parts in working order. Don’t improvise; call upon professionals.
Homemade repairs or welding
Homemade repairs, self-repairs, in-house repairs, DIY repairs: no matter what you call them, these repairs are discouraged since they often fail to meet the requirements outlined in the design codes. For instance, the Guidelines for the Assessment and Repair or Replacement of Damaged Rack issued by the Rack Manufacturers Institute (RMI) in the United States say that all welding should be performed by a certified welder and overseen by a qualified professional engineer.
It is also important to meet the appropriate specifications outlined by the American Welding Society (AWS), such as in AWS D1.1, where factors such as operating temperatures and surface conditions must be considered. Inadequate welds can lead to dangerous situations since the rack’s load capacity has most likely been changed. For more information, read our article Field Welding on Racks - Why Homemade Repairs May be Risky and Unsafe.
Homemade repairs, such as the ones shown in Figures 3 and 4 below, are inadequate.
![]() |
![]() |
Figure 3. Inadequate field welding | Figure 4. Inadequate homemade rack repair |
Engineered rack repair kits
Rack repair kits are more reliable for addressing damage to upright columns or braces. Engineered rack repair kits like Damotech’s permanently repair and protect racks without decreasing load capacity. Designed and certified by engineers, they provide warehouses with a safe, heavy-duty solution to rack damage. On top of that, they can adapt to various rack configurations; their quick installation will reduce downtime and save you from having to unload most pallets, if not all.
But not all repair kits are created equal.While both engineered and generic pallet rack repair kits serve the fundamental purpose, Engineered kits are specifically designed to match the original specifications and load capacities of the damaged rack system, ensuring optimal performance and safety. In contrast, generic kits may offer a one-size-fits-all solution that might not perfectly align with the specific needs or structural requirements of different rack types, potentially compromising the system's integrity and safety.
When faced with a damaged pallet rack component, there are 2 recommended courses of action: replace or repair. The first solution completely replaces the damaged component with an identical replacement part. The second is to repair the rack with an engineered rack repair solution. Damotech’s column repair kits can be a good alternative to replacing entire uprights and will restore the rack’s original load capacity while making it much more resistant to future impacts. Our adjustable brace is also a quick and easy solution to replacing damaged or missing horizontal or diagonal braces.
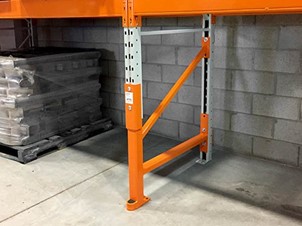
Figure 5. This column was repaired with a DAMO PRO. The rack's load capacity has, therefore, been restored.
Key takeaways on how rack beam levels affect load capacity
The key point to take away from this article is that any changes made to a pallet rack system will likely affect its load capacity. Therefore, a qualified racking expert should always be contacted beforehand. It is important to follow the configurations displayed on your LARCs or have new ones created. Non-matching configurations will invalidate existing load capacities, and new calculations will be required.
Lastly, rack repairs should always be performed with the help of professional installers to ensure the complete restoration of a pallet rack’s capacity.