Pallet racks play a crucial role in the efficiency of your warehouses and distribution centers. When used safely, they optimize storage space and allow fast and easy retrieval of stored goods.
The size and complexity of storage systems vary significantly from one warehouse to another. Despite the variations between structures, one fact remains: pallet racking systems comprise many components that, when put together, contribute to their stability and integrity.
When your pallet racks are damaged, it can be challenging to address the situation if you don't know the exact name of the affected component. Lack of knowledge makes online searches for replacement parts or repair solutions more difficult.
This article will help you identify every storage rack component and help you proactively address issues you may be experiencing with them.
Pallet rack upright, columns and braces
A pallet rack consists of uprights, which are themselves made up of various components:
Upright columns or posts
These are the two vertical components to which the braces are welded. The pallet racking beams are also attached to them to create the appropriate space for loading the pallets.
Horizontal and diagonal braces
These components connect the upright columns. Configured to increase the stability of the pallet rack system, the braces vary in number depending on the ladder's height.
Given their pivotal role in the stability of a rack, braces that have become deformed due to damage should be closely monitored.
Upright (ladder)
The overall structure you get by combining the two upright columns (front and rear) and the braces is called an upright. The depth and height of an upright can vary depending on the type of storage system.
Baseplates and anchors
Baseplates
Baseplates are welded to the base of a racking column or repair unit to distribute the weight of the racking on the ground and allow it to be securely anchored to the concrete floor with anchor bolts.
Anchors (or anchor bolts)
These are used to secure the pallet rack system to the building floor and maintain its position. Standards require that the racking system be anchored to the floor with at least one anchor per baseplate. Anchors can be either screw or wedge type.
The anchors allow the racking system to withstand displacements by the accidental impact of forklifts or by external forces such as earthquakes or wind.
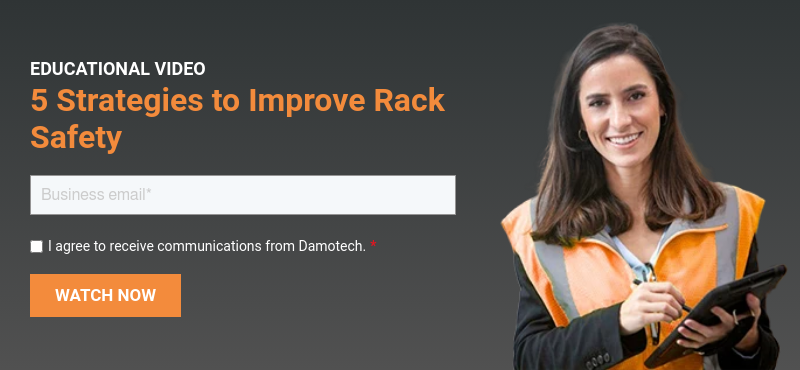
Beams, beam clips, and safety bars
Beams
Beams are the horizontal structural components that link two uprights in a pallet racking system. They support the weight of stored loads (often palletized) and transfer it to the rack columns to which they are connected. To ensure the integrity of your pallet racking system, monitoring the pallet rack beam deflection or sagging when heavy loads are placed on them is essential.
Beam clips
The beams are attached to the columns with beam clips. Beam clips are mostly specific to each manufacturer and should not be used on other racks unless approved by the manufacturer or rack engineer.
Rack safety bars
Safety bars are supported by the pallet racks' front and rear beams and are intended to support temporarily misplaced pallets. Although optional, they are recommended to help prevent falling pallets. They can help prevent accidents that seriously injure employees and damage merchandise or storage systems.
Rack bay
A bay is the space between two vertical uprights in a pallet rack system.
Load capacity plaques
Typically placed at the end of an aisle, the load capacity plaque is a method of signage intended to indicate the rated load capacity of the rack and the maximum weight it can hold.
It should include the maximum beam capacity, bay load, and the rack manufacturer's information. Moreover, a reference to drawing(s) or other approved documents that establish the maximum permissible load for a given rack bay can be included on the plaque. It should be placed where operators can read it. If all the information in the load plaque is standard for a bay, aisle, or rack section, one plaque is sufficient for that area.
Rack cell
A cell is a compartment or space between two columns on the same beam level, which usually accommodates two pallet positions.
Learning component names helps with safety and maintenance
Given the fast pace of operations, damage to storage systems is inevitable in all warehouses. The safety of your employees, merchandise, materials, and the building depends on paying close attention to your pallet racking systems because the risk of collapse increases when their integrity is affected.
Being able to name racking parts and components enables you and your team to communicate clearly regarding rack issues that might arise. Better decisions can be made about repairing or replacing the damaged components.
Stay one step ahead, and ensure professionals or engineers regularly inspect your racks. Get more info from Damotech on annual inspections.
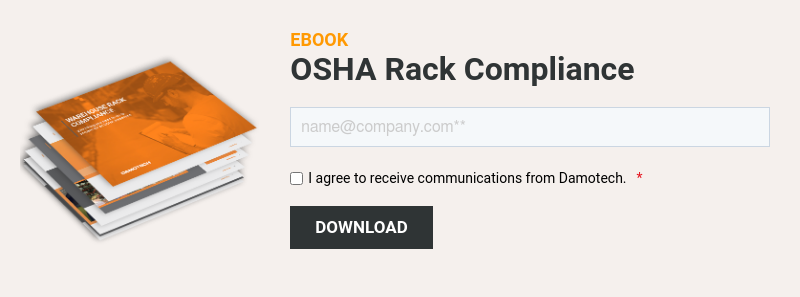
- Top 100 Warehouse Safety Quotes for Toolbox Talks, Posters & Meetings
- Top 12 Largest Warehouses in North America (Size, Tech & Safety)
- Costco’s Supply Chain Strategy: Decoding Its Warehousing Approach
- Minimum Distances Between Pallets, Rack Systems & Building Structures
- IKEA Warehouses: Efficient Warehousing and Distribution Strategies