Pallet rack footplates, also known as baseplates, may seem like a small component, but they play a vital role in the structural integrity and safety of a racking system. Baseplate damage can compromise your entire system, leading to instability, inefficiency, and even dangerous collapses. Whether due to forklift impacts, corrosion, or low-quality materials, addressing footplate issues promptly is vital for maintaining safety and compliance.
This blog will help you identify common footplate issues, understand their impact, and implement effective repair and protection solutions.
4 Reasons Pallet Rack Footplates Are Important
As the name suggests, a footplate sits at the base of a racking system. As a pallet racking system comprises vertical stacks of goods, stabilizing it is paramount. Footplates sit at the bottom of a racking system, holding it firm to the ground. They also boost the overall stability of the rack by serving as the anchor point. The columns are attached to the floor by bolts that go through these footplates.
A pallet rack footplate serves several key functions:
- Distributes column loads over a larger area.
- Provides a connection surface to anchor uprights to the floor.
- Allows the placement of shims to keep the racking system plumb, as deviations from plumb can compromise stability.
- Keeps the racking system in place during seismic events, which can cause warehouse racking to collapse.
- Designed to resist forces at the base of columns (along with anchors).
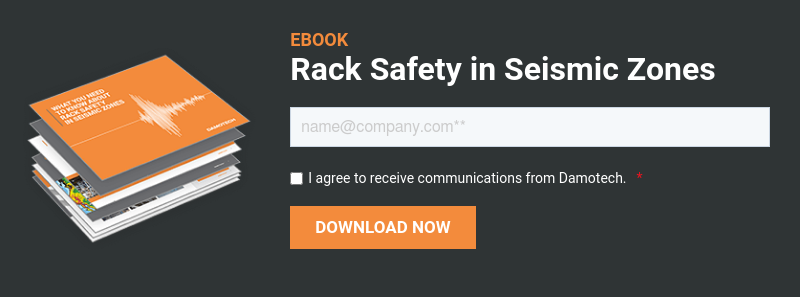
A Key Risk Factor for Your Warehouse Racking System
A damaged pallet rack footplate can put your pallet rack system at risk. Aweakened baseplate compromises the overall stability of the system.
A strong baseplate helps keep the system’s structure intact upon collision, reducing the risks of critical occurrences like collapses. Pallet rack footplates also serve to transfer the load to the ground, keeping the entire racks in place.
Importance of Shims
Shims are thin, durable steel plates placed under the pallet rack footplates to compensate for uneven concrete floors. Their primary purpose is to ensure that the racking system remains plumb and stable. It is important to note that CSA (Canada) codes require shims to match the baseplate dimensions, while ANSI (USA) codes allow shims to be equal to or larger than the baseplate dimensions.
Functions of Shims in Racking Systems:
- Correcting Floor Irregularities: Shims help level the baseplates when the floor is uneven, preventing tilting.
- Maintaining Plumb Alignment: A properly shimmed upright ensures the rack stays within acceptable out-of-plumb tolerances, reducing the risk of collapse.
- Ensuring Proper Load Distribution: By keeping the baseplate in full contact with the floor, shims help evenly distribute the load, minimizing stress on anchors and the concrete surface.
How to Diagnose Pallet Rack Footplate Damage
Like every other metal component, baseplates are vulnerable to damage over time. This damage could result from mishandling, i.e., incorrect or inefficient use of the racking system, accidental damage from impacts, or common causes of baseplate damage.
1. Impact Damage
Impact from forklifts is the primary source of damage to footplates. It is essential to inspect for impact damage of this type regularly, monthly, or quarterly, depending on the size of your warehouse. Look for deflection caused by impacts. Deflection is where the anchor plate is twisted or pushed back from its correct square alignment. As always, the Rack Manufacturer’s Institute (RMI) standards suggest a qualified inspector should do official inspections of all damage.
2. Exposure to Corrosion and Rust
Over time, the properties of many metals tend to degrade. These degradations include appearance, loss of strength, and increased permeability to different gases and liquids. This degradation is known as corrosion.
Corrosion occurs when metal is exposed to external environmental factors like acids, bases, water, oils, and other chemicals in solid or liquid forms. Like every metal component, footplates are vulnerable to corrosion, especially in rugged industrial environments where the above-mentioned factors are present in abundance.
Rust is a type of corrosion that’s specifically tied to the oxidation of iron or its alloys. When exposed to oxygen and moisture, iron and its alloys form a reddish-brown substance called rust. Rusting might start from one segment of the metallic piece and eventually spread to disintegrate the entire component.
Footplates made of iron and its alloys could degrade in quality because of rust over time due to prolonged exposure to moisture. A racking system’s overall strength and integrity might diminish tremendously if a major portion of the footplates suffers from rust or any other form of corrosion. Take note of any missing paint or covering of the steel.
3. Damaged Anchor Holes
The holes in the pallet rack footplates where the anchors are secured can become damaged over time due to impact, corrosion, or other factors. When inspecting column baseplates, it’s essential to analyze the condition of these anchor holes to ensure they are in good condition. Baseplates with damaged anchor holes should be replaced. During repair, it is advised to install the anchors in an alternative hole to ensure the proper installation of the new anchor.
4. Concrete Slab
Pallet rack footplates are anchored to a concrete slab to distribute the load and ensure the stability of the entire racking system. The quality of the concrete slab beneath the baseplate plays an important role in the performance of your racking system.
It is important to ensure that the concrete slab in your warehouse is designed to support the loads being applied. Over time, the floor underneath the baseplates can settle, causing rack performance issues. Concrete can also be damaged locally, causing anchoring issues or out-of-plumb uprights. As the foundation that supports your racks, it is important to ensure the concrete slab beneath the baseplates is in good condition.
5. Seismic Forces
As the integrity of a pallet racking system is linked to the pallet rack footplates, it is important to follow the rack manufacturer’s recommendations regarding baseplate size and thickness.
Warehouses situated in zones of high seismic activity have uprights that are typically designed to have larger, thicker baseplates. Depending on the geographical location of your facility, seismic forces can vary. RMI recommends consulting a professional engineer who is familiar with the design and construction of pallet racks to ensure that you have suitable racking components in your facility.
6. Weak or Loose Anchor Bolts
Anchor bolts are crucial components for any racking system. RMI typically recommends one anchor per footplate. However, depending on the warehouse location or specific application, the manufacturer or engineer can specify more than one anchor. Anchors keep the baseplate attached to the ground and the racking system in place. Both the quality of the concrete and the strength of anchor bolts play a key role in ensuring the safe operation of your racking system.
It is imperative to inspect anchor bolts routinely to ensure they are present and properly torqued according to the manufacturer’s specifications.
7. Sheared Welding Damage
Welds connecting the footplate to the column can be sheared off entirely or partially. For this reason, it is important to look out for this type of damage. Pay special attention when inspecting for damage to the weld points on your footplates for corrosion and shearing.
Practical Solutions for Pallet Rack Footplates
To keep your racking system intact:
-
Have footplates and the racking system inspected routinely, depending on your warehouse’s use patterns and conditions.
-
Be sure to check front and back footplates and move materials if they obstruct your view.
-
Ensure professional inspections are done to RMI standards by an experienced inspector.
-
Ensure all upright columns are equipped with at least one anchor (more if required).
-
Ensure the concrete slab in your warehouse is capable of supporting the applied loads. If you are unsure or if the loads have changed, it’s advisable to contact a professional engineer.
- When repairing or replacing an upright, ensure the proper baseplate size and thickness is used based on the location of your facility.
Act Now: Rack Repair and Protection to Prevent Future Failures
Another way to prevent pallet rack footplate damage in key high-traffic areas is to use Damotech pallet rack guards. These protection solutions surround your footplates with solid steel independently anchored to the concrete floor. The impact will be diverted and absorbed by the end of the aisle guards or the column guards. This is a solid strategy to keep your warehouse running to maximum efficiency and reduce the need for repairs. Our experts can help you lay out a plan for protecting your warehouse.
Don’t put off the inspection and repair process before it is too late. Make rack repair and inspection a routine part of your warehouse operations. At Damotech, our experts are here to help you safeguard your warehouse. If you need more clarification about the state of your footplates or need professional guidance, feel free to contact us.
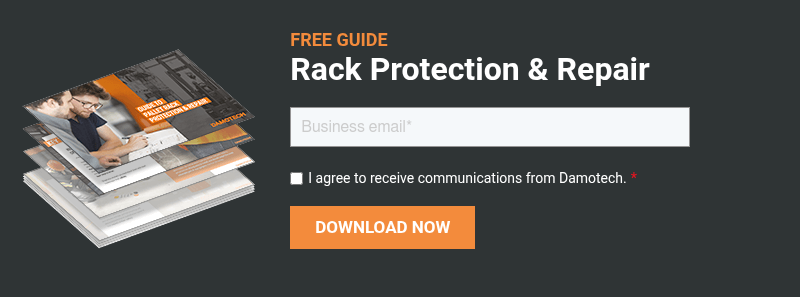
- Top 12 Largest Warehouses in North America (Size, Tech & Safety)
- Top 100 Warehouse Safety Quotes for Toolbox Talks, Posters & Meetings
- Costco’s Supply Chain Strategy: Decoding Its Warehousing Approach
- Minimum Distances Between Pallets, Rack Systems & Building Structures
- IKEA Warehouses: Efficient Warehousing and Distribution Strategies